PRODUCT PARAMETERS
Description
Overview of Factory Custom Molded High Precision Plastic Gears With Metal Hubs For High-Torque Applications
Gears are mechanical elements that are typically used to transmit rotational motion and force. They work by meshing teeth with each other to change speed, direction of torque, or to transfer power between multiple shafts. Gears are an integral part of mechanical engineering and are widely used in a variety of mechanical devices.
Advantages and features of Factory Custom Molded High Precision Plastic Gears With Metal Hubs For High-Torque Applications
Efficient transmission: Gears are capable of directly converting power with high efficiency and low energy loss.
Precise ratios: the desired ratio of speed and torque can be obtained by selecting gears of different sizes.
Compact: Factory Custom Molded High Precision Plastic Gears With Metal Hubs For High-Torque Applicationssystems take up less space than other forms of power transmission.
High durability: well-designed gears can operate stably for long periods of time in harsh environments.
Low noise and vibration: Modern Factory Custom Molded High Precision Plastic Gears With Metal Hubs For High-Torque Applicationsmanufacturing technology ensures smooth operation and reduces noise and vibration.
Various types: Spur, helical, and bevel gears are available depending on the application scenario.
(Factory Custom Molded High Precision Plastic Gears With Metal Hubs For High-Torque Applications)
Specifications of Factory Custom Molded High Precision Plastic Gears With Metal Hubs For High-Torque Applications
Factory Custom Molded High Precision Plastic Gears with Metal Hubs are engineered to deliver exceptional performance in high-torque applications. These gears are designed to meet the demanding requirements of industries such as automotive, robotics, industrial machinery, and consumer electronics. The combination of high-strength plastic materials and precision-machined metal hubs ensures durability, reliability, and optimal functionality under heavy loads and high-stress conditions.
The gears are manufactured using advanced injection molding techniques, ensuring tight tolerances and consistent quality. The plastic components are made from high-performance engineering plastics such as POM (Polyoxymethylene), nylon, or PEEK, which offer excellent wear resistance, low friction, and high dimensional stability. The metal hubs, typically made from stainless steel, aluminum, or brass, provide enhanced strength and rigidity, ensuring a secure fit and long-lasting performance.
These custom gears are available in a wide range of sizes, tooth profiles, and configurations to suit specific application needs. They can be designed with spur, helical, bevel, or worm gear profiles, depending on the required torque transmission and operational efficiency. The precision molding process ensures smooth operation, minimal noise, and reduced vibration, making them ideal for applications where quiet and efficient performance is critical.
Key features include high load-bearing capacity, resistance to corrosion and chemicals, and the ability to operate in a wide temperature range. The metal hubs are precision-machined to ensure perfect alignment and seamless integration with shafts or other components. Additionally, these gears can be customized with specific surface finishes, coatings, or lubrication options to further enhance performance and longevity.
Whether used in heavy-duty industrial equipment or precision-driven systems, Factory Custom Molded High Precision Plastic Gears with Metal Hubs offer a cost-effective, lightweight, and durable solution for high-torque applications. Their ability to withstand extreme conditions while maintaining precision and reliability makes them a preferred choice for engineers and designers seeking high-performance gear solutions.
(Factory Custom Molded High Precision Plastic Gears With Metal Hubs For High-Torque Applications)
Applications of Factory Custom Molded High Precision Plastic Gears With Metal Hubs For High-Torque Applications
Factory custom molded high precision plastic gears with metal hubs are engineered to meet the demanding requirements of high-torque applications across various industries. These gears combine the lightweight, corrosion-resistant, and cost-effective properties of high-performance plastics with the strength and durability of metal hubs, making them ideal for applications where reliability and precision are critical. The metal hubs provide enhanced structural integrity, ensuring the gears can withstand high torque loads without compromising performance.
One of the primary applications of these gears is in the automotive industry, where they are used in transmission systems, steering mechanisms, and electric vehicle components. Their ability to operate smoothly under high stress and resist wear makes them a preferred choice for improving efficiency and reducing maintenance costs. Additionally, their lightweight nature contributes to overall vehicle weight reduction, enhancing fuel efficiency.
In industrial machinery, these gears are widely used in robotics, conveyor systems, and heavy-duty equipment. Their high precision ensures accurate motion control, while the metal hubs provide the necessary strength to handle heavy loads and repetitive operations. This combination makes them suitable for applications requiring long-term durability and minimal downtime.
The medical industry also benefits from these gears, particularly in diagnostic equipment, surgical tools, and imaging devices. Their precision and smooth operation are essential for ensuring accurate results and patient safety. The use of high-performance plastics also allows for sterilization, making them suitable for medical environments.
In the aerospace sector, these gears are utilized in flight control systems, landing gear mechanisms, and satellite components. Their lightweight design helps reduce overall aircraft weight, while their ability to withstand extreme temperatures and harsh conditions ensures reliable performance in critical applications.
Overall, factory custom molded high precision plastic gears with metal hubs offer a versatile and reliable solution for high-torque applications across multiple industries. Their unique combination of materials and precision engineering ensures optimal performance, durability, and cost-effectiveness, making them an essential component in modern machinery and equipment.
Campony Introduction
Established in 2002, Shift Gear Machinery Co.,ltd. focus on metal research and mining machinery spare parts. 2 factories over an area of 13,300 square meters, based on 100+ sets of equipment, our production capacity reaches 12000 Tons/Year. has passed ISO 9001 quality managment system certification in 2008.
Our mainly products are dragline excavator spare parts,rotary kiln spare parts, large modulus gear (gear shaft), gearbox ect. 40+ patents with over 45 years experience to help focus on improve the service life of spare parts. We belive that more than 80% reason of mechanical parts’ working life depends on hot processing (steel making/forging/casting/welding/heat treatment). Eight material engineers will control the quality from the original resource.
If you are interested, please feel free to contact us.
Payment
L/C, T/T, Western Union, Paypal, Credit Card etc.
Shipment
By sea, by air, by express, as customers request.
5 FAQs of Factory Custom Molded High Precision Plastic Gears With Metal Hubs For High-Torque Applications
When it comes to high-torque applications, factory custom molded high precision plastic gears with metal hubs are a popular choice due to their durability, efficiency, and cost-effectiveness. Here are five frequently asked questions about these specialized gears:
1. **What are the advantages of using plastic gears with metal hubs?**
Plastic gears with metal hubs combine the lightweight and corrosion-resistant properties of plastic with the strength and rigidity of metal. The plastic teeth reduce noise and wear, while the metal hub provides enhanced load-bearing capacity and torque transmission. This combination makes them ideal for high-torque applications where precision and durability are critical.
2. **What materials are used for the plastic gears and metal hubs?**
The plastic gears are typically made from high-performance engineering plastics such as POM (polyoxymethylene), nylon, or PEEK, which offer excellent wear resistance and low friction. The metal hubs are often crafted from stainless steel, aluminum, or brass, depending on the application’s requirements for strength, weight, and corrosion resistance.
3. **Can these gears be customized for specific applications?**
Yes, these gears are fully customizable. Manufacturers can tailor the gear design, tooth profile, size, and material to meet the exact needs of your application. Whether you need gears for automotive, industrial machinery, or medical devices, custom solutions ensure optimal performance and longevity.
4. **How do these gears perform in high-torque applications?**
Plastic gears with metal hubs are engineered to handle high-torque demands efficiently. The metal hub provides a robust connection to the shaft, ensuring minimal slippage and maximum torque transfer. The precision-molded plastic teeth are designed to withstand repetitive stress and reduce the risk of failure under heavy loads.
5. **What industries commonly use these gears?**
These gears are widely used in industries such as automotive, aerospace, robotics, medical devices, and industrial machinery. Their ability to deliver high precision, low noise, and reliable performance makes them suitable for applications ranging from power transmission systems to precision motion control.
In summary, factory custom molded high precision plastic gears with metal hubs are a versatile and reliable solution for high-torque applications. Their unique combination of materials and customization options ensures they meet the demanding requirements of various industries.
(Factory Custom Molded High Precision Plastic Gears With Metal Hubs For High-Torque Applications)
REQUEST A QUOTE
RELATED PRODUCTS
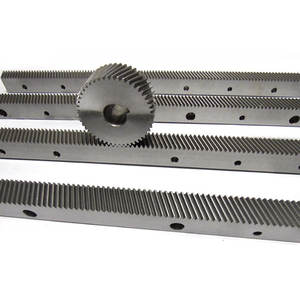
Custom Manufacture Black Plastic Rack Gears Custom Gear Manufacturing
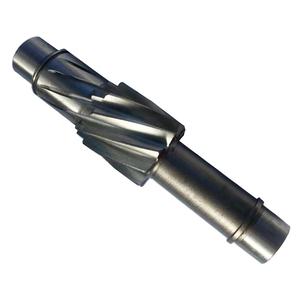
3F FAMED Gear Harmonic Reducer CSG|CSF 17-120 Harmonic Drive Gearbox with Motor
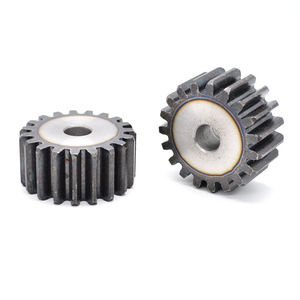
In Volkswagen Motor Gear Lever Disassembly Tool

Manufactory Direct Not Easy To Wear Good Transmission Rate Engine Gear For Construction Machinery

Metallurgy powder customized High precision Stainless Steel Iron bronze Sintered plastic drive gear and spur gear
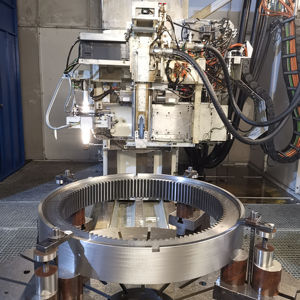