PRODUCT PARAMETERS
Description
Overview of Custom Precision Cnc Machining Parts Large Diameter Gerber Spur Gears For Gear Transmission
Gears are mechanical elements that are typically used to transmit rotational motion and force. They work by meshing teeth with each other to change speed, direction of torque, or to transfer power between multiple shafts. Gears are an integral part of mechanical engineering and are widely used in a variety of mechanical devices.
Advantages and features of Custom Precision Cnc Machining Parts Large Diameter Gerber Spur Gears For Gear Transmission
Efficient transmission: Gears are capable of directly converting power with high efficiency and low energy loss.
Precise ratios: the desired ratio of speed and torque can be obtained by selecting gears of different sizes.
Compact: Custom Precision Cnc Machining Parts Large Diameter Gerber Spur Gears For Gear Transmissionsystems take up less space than other forms of power transmission.
High durability: well-designed gears can operate stably for long periods of time in harsh environments.
Low noise and vibration: Modern Custom Precision Cnc Machining Parts Large Diameter Gerber Spur Gears For Gear Transmissionmanufacturing technology ensures smooth operation and reduces noise and vibration.
Various types: Spur, helical, and bevel gears are available depending on the application scenario.
(Custom Precision Cnc Machining Parts Large Diameter Gerber Spur Gears For Gear Transmission)
Specifications of Custom Precision Cnc Machining Parts Large Diameter Gerber Spur Gears For Gear Transmission
Personalized Precision CNC Machining Parts Large Diameter Gerber Spur Gears for Equipment Transmission are engineered to supply high performance, durability, and precision in demanding industrial applications. These gears are made using innovative CNC machining modern technology, ensuring limited tolerances, premium surface area coating, and constant top quality. Suitable for sturdy transmission systems, they are developed to handle high torque, rotational speeds, and operational tensions.
** Material Options: ** Available in high-strength products such as carbon steel (e.g., 1045, 4140), stainless steel (303, 304, 316), alloy steel (4340, 8620), and specialized metals like brass or aluminum. Material selection is customized to application requirements, consisting of corrosion resistance, use resistance, and load-bearing ability.
** Dimensions & Tolerances: ** Personalized sizes varying from 500mm to 3000mm, with densities up to 500mm. Gear teeth are machined to AGMA (American Gear Manufacturers Organization) or ISO standards, making sure accurate meshing and very little reaction. Regular tolerances follow ISO 2768-mK requirements, with equipment tooth profiles held to IT6-IT8 precision qualities.
** Tooth Profile & Specs: ** Stimulate gears include a straight-tooth layout with stress angles of 20 ° (standard) or 25 ° (for high-load applications). Components vary from 10 to 50, with personalized pitch diameters, bore sizes, and keyway arrangements. Teeth are hardened using warmth therapy (e.g., carburizing, induction hardening) to attain surface area firmness of 45-60 HRC for enhanced wear resistance.
** Surface Area Finish & Coatings: ** Machined surfaces attain Ra 0.8– 3.2 μm roughness. Optional layers include black oxide, zinc plating, nickel, or PTFE for corrosion protection, lowered rubbing, and prolonged service life.
** Load Capability: ** Engineered for static loads up to 50,000 N · m and dynamic tons exceeding 30,000 N · m, depending upon product and style. Customized equipment styles fit specific torque, RPM, and environmental problems (e.g., heats, rough environments).
** Applications: ** Extensively utilized in mining devices, concrete plants, wind turbines, aquatic propulsion systems, and heavy machinery where trusted power transmission is crucial.
** Personalization: ** Tailored to customer specs, including non-standard birthed patterns, flange places, or integrated hubs. Prototyping and set production sustained, with complete CAD/CAM documentation and high quality qualifications (ISO 9001, RoHS).
** Quality Assurance: ** Each gear goes through rigorous evaluation using CMM (Coordinate Gauging Device), gear testers, and ultrasonic testing to verify dimensional accuracy, tooth profile stability, and product consistency.
These Gerber spur gears guarantee smooth integration right into transmission systems, offering long life, effectiveness, and decreased maintenance for commercial procedures.
(Custom Precision Cnc Machining Parts Large Diameter Gerber Spur Gears For Gear Transmission)
Applications of Custom Precision Cnc Machining Parts Large Diameter Gerber Spur Gears For Gear Transmission
Personalized accuracy CNC machining components, such as huge size Gerber stimulate gears, play a crucial duty in modern-day gear transmission systems across varied industries. These equipments are engineered to supply high torque, smooth procedure, and outstanding durability, making them excellent for durable applications where reliability and accuracy are non-negotiable. Gerber stimulate gears, identified by their straight teeth and parallel shaft alignment, are particularly created for efficient power transmission in systems needing big rotational force and very little reaction.
Among the key applications of custom-made huge diameter Gerber stimulate equipments is in hefty machinery and industrial tools. Industries like mining, building, and product handling rely upon these equipments for conveyor systems, crushers, and excavators, where they ensure regular performance under extreme lots. Their precision-machined teeth minimize wear and sound, boosting functional effectiveness and durability.
The energy market also benefits from these gears, especially in wind turbines and hydroelectric power plants. Big diameter Gerber spur equipments are important to gearboxes that convert low-speed blades motion into high-speed generator turning. CNC machining makes sure tight resistances, vital for keeping placement and decreasing energy loss in these high-stakes settings.
In the automotive and aerospace industries, customized Gerber stimulate equipments are made use of in specialized transmission systems, screening rigs, and landing gear systems. Their capacity to deal with high tension and repeated activity makes them suitable for applications requiring light-weight yet durable components. CNC machining allows for personalization in materials, such as alloy steels or aerospace-grade aluminum, customized to particular thermal and mechanical requirements.
An additional vital benefit of CNC-machined Gerber stimulate equipments is their adaptability. Manufacturers can produce gears with sizes exceeding numerous meters while keeping micron-level precision. This personalization sustains unique applications, such as aquatic propulsion systems or large production automation, where off-the-shelf solutions fall short. Surface therapies like nitriding or hardening even more improve wear resistance and deterioration protection.
By leveraging CNC machining, businesses achieve equipments that incorporate perfectly into existing systems, minimize downtime, and enhance power transmission performance. Whether for industrial, power, or transportation applications, personalized big size Gerber spur equipments stand for a fusion of precision design and useful flexibility, driving efficiency in the most requiring environments.
Campony Introduction
Established in 2002, Shift Gear Machinery Co.,ltd. focus on metal research and mining machinery spare parts. 2 factories over an area of 13,300 square meters, based on 100+ sets of equipment, our production capacity reaches 12000 Tons/Year. has passed ISO 9001 quality managment system certification in 2008.
Our mainly products are dragline excavator spare parts,rotary kiln spare parts, large modulus gear (gear shaft), gearbox ect. 40+ patents with over 45 years experience to help focus on improve the service life of spare parts. We belive that more than 80% reason of mechanical parts’ working life depends on hot processing (steel making/forging/casting/welding/heat treatment). Eight material engineers will control the quality from the original resource.
If you are interested, please feel free to contact us.
Payment
L/C, T/T, Western Union, Paypal, Credit Card etc.
Shipment
By sea, by air, by express, as customers request.
5 FAQs of Custom Precision Cnc Machining Parts Large Diameter Gerber Spur Gears For Gear Transmission
What are Gerber Spur Gears, and where are they commonly used? Gerber Spur Gears are large-diameter, high-precision gears designed for efficient power transmission in heavy-duty applications. They feature a straight-tooth profile, ensuring smooth engagement and uniform load distribution. These gears are widely used in industries requiring robust torque handling, such as mining equipment, wind turbines, marine propulsion systems, and industrial machinery. Their large diameter (often exceeding 1 meter) makes them ideal for applications demanding high rotational stability and minimal backlash.
Why choose CNC machining for manufacturing large-diameter Gerber Spur Gears? CNC machining ensures exceptional accuracy, repeatability, and surface finish, critical for gears that operate under high stress. Advanced CNC mills and lathes can handle oversized workpieces, maintaining tight tolerances (up to ±0.005 mm) even for complex geometries. This process minimizes human error, enhances durability, and supports customization for unique tooth profiles, bore sizes, or mounting configurations. CNC machining also allows efficient production of prototypes and bulk orders, reducing lead times.
What materials are typically used for these gears? Common materials include high-strength alloy steels (e.g., 4140, 4340), stainless steel (304/316), and brass for corrosion resistance. For lightweight applications, aluminum or engineered plastics like PEEK may be used. Material selection depends on load capacity, environmental conditions (e.g., moisture, temperature), and wear resistance requirements. Heat treatment processes like carburizing or nitriding are often applied to enhance surface hardness and longevity.
How is precision ensured during production? Precision is achieved through multi-axis CNC machines, CAD/CAM software for exact design replication, and rigorous quality checks. Post-machining, gears undergo coordinate measuring machine (CMM) inspections, hardness testing, and gear profile analysis via laser scanners. Surface finish is verified to reduce friction, and runout testing ensures concentricity. Certifications like ISO 9001 guarantee adherence to international standards.
Can Gerber Spur Gears be customized, and what is the typical lead time? Yes, customization options include tooth modulus, pitch diameter, bore type (keyway, spline), and coating (e.g., zinc, black oxide). Engineers collaborate with clients to adjust designs for specific torque, speed, or noise reduction needs. Lead times vary from 2–8 weeks, depending on gear size, material availability, and order volume. Rush services are often available for urgent projects without compromising quality.
(Custom Precision Cnc Machining Parts Large Diameter Gerber Spur Gears For Gear Transmission)
REQUEST A QUOTE
RELATED PRODUCTS
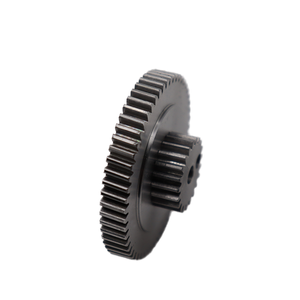
Linyao factory large forged high quality steel custom made internal gear for mechanical equipment
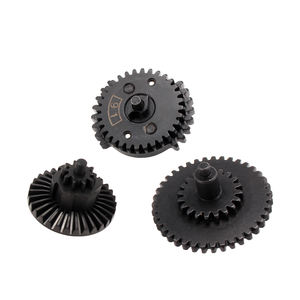
8223072 Gear Selector Transmission Controller Transmission Shifter For Engine Diesel Excavator Spare Parts

Aluminum Alloy Stainless Steel Wheel Accessories Primary Gear Wheel Bearing Gear

China whole pinion gear differential ring CNC machining parts differential ring and pinion gears

Whole Car Parts for Korean Cars 56500-C5000 Steering Gear Box for KIA SORENTO III 2015-2020 LHD Steering Rack 56500-C5001
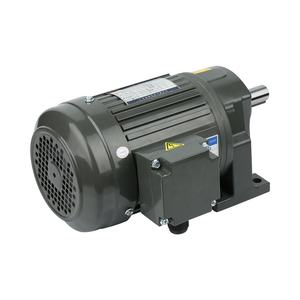