PRODUCT PARAMETERS
Description
Overview of Mass Production High Performance Custom Plastic-Metal Hybrid Gears For Industrial
Gears are mechanical elements that are typically used to transmit rotational motion and force. They work by meshing teeth with each other to change speed, direction of torque, or to transfer power between multiple shafts. Gears are an integral part of mechanical engineering and are widely used in a variety of mechanical devices.
Advantages and features of Mass Production High Performance Custom Plastic-Metal Hybrid Gears For Industrial
Efficient transmission: Gears are capable of directly converting power with high efficiency and low energy loss.
Precise ratios: the desired ratio of speed and torque can be obtained by selecting gears of different sizes.
Compact: Mass Production High Performance Custom Plastic-Metal Hybrid Gears For Industrialsystems take up less space than other forms of power transmission.
High durability: well-designed gears can operate stably for long periods of time in harsh environments.
Low noise and vibration: Modern Mass Production High Performance Custom Plastic-Metal Hybrid Gears For Industrialmanufacturing technology ensures smooth operation and reduces noise and vibration.
Various types: Spur, helical, and bevel gears are available depending on the application scenario.
(Mass Production High Performance Custom Plastic-Metal Hybrid Gears For Industrial)
Specifications of Mass Production High Performance Custom Plastic-Metal Hybrid Gears For Industrial
Our mass-produced high-performance personalized plastic-metal crossbreed gears are developed for commercial applications. These equipments integrate resilient steel parts with advanced design plastics. The hybrid style makes sure stamina, minimized weight, and resistance to wear. They handle high loads and run efficiently in demanding atmospheres.
The equipments use metals like stainless-steel or aluminum for vital tension areas. Design plastics such as PEEK or nylon are incorporated for noise decrease and deterioration resistance. This mix equilibriums resilience and performance. Personalized equipment styles are readily available to match details torque, rate, and ecological demands.
Accuracy molding and machining methods produce limited tolerances. Teeth accounts are optimized for very little friction and optimum power transfer. Surface area treatments like solidifying or finishes enhance durability. Lubrication-free options are feasible because of low-friction plastic composites.
Production includes automated injection molding and CNC machining. This guarantees uniformity throughout huge batches. Quality checks consist of anxiety screening, dimensional confirmation, and real-world simulation. Each gear fulfills ISO standards for performance and safety and security.
These hybrid gears match robotics, automotive systems, hefty equipment, and conveyor arrangements. They perform in high-temperature, humid, or chemically subjected setups. Custom-made sizes vary from little accuracy gears (under 10mm diameter) to large commercial components (over 500mm).
Choices include customized tooth profiles, birthed forms, and installing setups. Materials can be changed for particular thermal or chemical conditions. Load capacities reach up to 15,000 Nm. Functional temperatures vary from -40 ° C to 150 ° C. Sound degrees remain below 65 dB in many setups.
In reverse compatibility with existing metal gear systems is feasible. Crossbreed gears decrease upkeep costs and power use contrasted to traditional all-metal versions. Technical support assists with design assimilation and performance testing. Preparations for mass production start at four weeks. Customized prototypes are readily available for testing before major orders.
The equipments ship in safety packaging to avoid damages throughout transit. Bulk order discounts make an application for amounts above 1,000 units. Detailed specification sheets and CAD documents are provided for engineering testimonial.
(Mass Production High Performance Custom Plastic-Metal Hybrid Gears For Industrial)
Applications of Mass Production High Performance Custom Plastic-Metal Hybrid Gears For Industrial
Mass production high-performance customized plastic-metal crossbreed gears are utilized in lots of markets. These equipments incorporate plastic parts with steel cores. The mix gives strength from steel and adaptability from plastic. They take care of heavy tons and last much longer. Factories utilize them because they are reputable and cost much less than all-metal equipments.
Automotive manufacturers make use of these equipments in electrical lorries and transmission systems. The plastic components reduced weight and noise. This assists cars and trucks make use of less gas and run smoother. Metal cores ensure equipments remain strong under tension. Hybrid gears work well in tight areas. They fit contemporary auto designs that require little components.
Industrial makers like conveyor belts and packaging equipment depend on hybrid gears. The plastic parts withstand chemicals and water. Metal components deal with high stress. Machines run much longer without picking up repairs. Factories save money on maintenance. Assembly line stay energetic a lot more hours each day.
Robotics firms choose hybrid equipments for precise movements. Plastic layers minimize vibration. Steel bases maintain shapes exact throughout quick spins. Robots make less mistakes in setting up tasks. These gears help robots operate in health centers or storehouses without damaging down.
Aerospace engineers choose hybrid gears for aircraft systems. Less weight matters in aircrafts and drones. Plastic-metal equipments survive temperature changes much better than all-plastic kinds. They operate in landing gear mechanisms and trip control systems. Planes stay safe while melting less fuel.
Customer electronics use little crossbreed gears in tools like printers and power tools. Plastic cuts manufacturing costs. Steel cores prevent gear teeth from wearing out. Gadget last much longer between replacements. Customers obtain peaceful procedure and smooth performance.
Crossbreed equipments support renewable energy projects as well. Wind generators use them in transmissions. Plastic parts deal with weather adjustments. Metal components manage torque from rotating blades. Turbines produce power steadily with much less downtime. Solar trackers make use of these equipments to comply with sunlight accurately.
Campony Introduction
Established in 2002, Shift Gear Machinery Co.,ltd. focus on metal research and mining machinery spare parts. 2 factories over an area of 13,300 square meters, based on 100+ sets of equipment, our production capacity reaches 12000 Tons/Year. has passed ISO 9001 quality managment system certification in 2008.
Our mainly products are dragline excavator spare parts,rotary kiln spare parts, large modulus gear (gear shaft), gearbox ect. 40+ patents with over 45 years experience to help focus on improve the service life of spare parts. We belive that more than 80% reason of mechanical parts’ working life depends on hot processing (steel making/forging/casting/welding/heat treatment). Eight material engineers will control the quality from the original resource.
If you are interested, please feel free to contact us.
Payment
L/C, T/T, Western Union, Paypal, Credit Card etc.
Shipment
By sea, by air, by express, as customers request.
5 FAQs of Mass Production High Performance Custom Plastic-Metal Hybrid Gears For Industrial
What are plastic-metal hybrid gears?
Plastic-metal hybrid gears combine plastic parts with metal components. The metal parts handle high stress areas. The plastic parts cut weight and noise. This mix improves performance in tough conditions. They last longer than standard plastic gears. They work better than metal gears in some cases.
Why choose plastic-metal hybrid gears for industrial use?
These gears offer strength and light weight. They handle heavy loads without breaking. They reduce energy use by being lighter. Less vibration means machines run smoother. Maintenance costs drop because they wear slower. They fit many industrial settings needing reliable parts.
What industries benefit most from these gears?
Automotive systems use them for transmissions and motors. Robotics need precise, quiet movement. Heavy machinery relies on their durability. Aerospace applications value weight savings. Medical devices use them for smooth operation. Any industry needing strong, efficient gears can benefit.
How customizable are these gears?
Designs adjust to fit exact needs. Choices include plastic type, metal grade, size, and tooth shape. Modifications suit specific loads or speeds. Prototypes test before mass production. Custom colors or coatings add extra protection. Changes ensure the gear works in your machine.
What is the production time for large orders?
Lead times depend on order size and design complexity. Standard designs ship faster. Mass production speeds up with molds ready. Rush options exist for urgent needs. Most orders finish in 4-6 weeks. Delays happen if designs need tweaks after testing.
(Mass Production High Performance Custom Plastic-Metal Hybrid Gears For Industrial)
REQUEST A QUOTE
RELATED PRODUCTS
transmission shaft oem custom metal milling stainless steel turning cnc machining shaft parts metal motor gear shaft
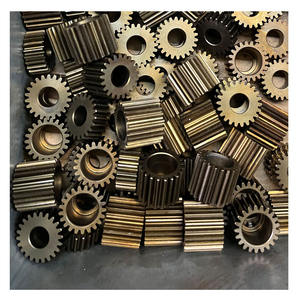
Foundry Metal Casting Service Grey Iron Ductile Iron Sand Casting gear box Cast iron Part CNC machining GGG40 GGG45 GGG50

China whole pinion gear differential ring CNC machining parts differential ring and pinion gears
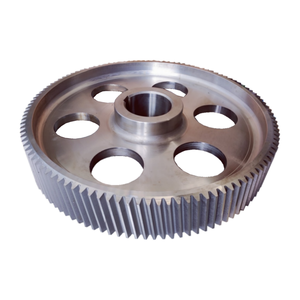
Comprehensive Custom Cnc Machining Precision Spur Gears Steel Gears And Oem Fabrications
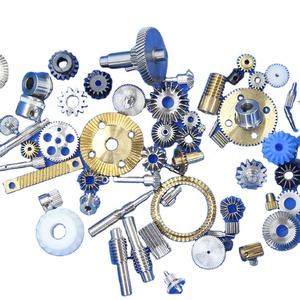
20CrMnTi Low carbon steel Forging large Crown gear large spiral bevel gear
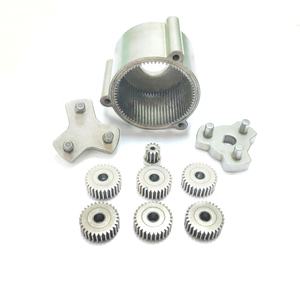