PRODUCT PARAMETERS
Description
Overview of CNC Machined High Ration Spiral Bevel Gear For Power Tool
Gears are mechanical elements that are typically used to transmit rotational motion and force. They work by meshing teeth with each other to change speed, direction of torque, or to transfer power between multiple shafts. Gears are an integral part of mechanical engineering and are widely used in a variety of mechanical devices.
Advantages and features of CNC Machined High Ration Spiral Bevel Gear For Power Tool
Efficient transmission: Gears are capable of directly converting power with high efficiency and low energy loss.
Precise ratios: the desired ratio of speed and torque can be obtained by selecting gears of different sizes.
Compact: CNC Machined High Ration Spiral Bevel Gear For Power Toolsystems take up less space than other forms of power transmission.
High durability: well-designed gears can operate stably for long periods of time in harsh environments.
Low noise and vibration: Modern CNC Machined High Ration Spiral Bevel Gear For Power Toolmanufacturing technology ensures smooth operation and reduces noise and vibration.
Various types: Spur, helical, and bevel gears are available depending on the application scenario.
(CNC Machined High Ration Spiral Bevel Gear For Power Tool)
Specifications of CNC Machined High Ration Spiral Bevel Gear For Power Tool
This item is a CNC-machined high-ratio spiral bevel equipment made for power devices. It makes certain efficient power transmission in small areas. The equipment takes care of high torque tons. It operates in demanding applications like electrical drills, angle grinders, and rotating saws. The spiral bevel layout boosts get in touch with in between teeth. This lowers noise throughout procedure. It additionally lessens resonance. The outcome is smoother performance under hefty use.
The gear is made from high-strength steel alloys. Typical products consist of 4140 steel or 304 stainless-steel. These options equilibrium longevity with corrosion resistance. Heat treatment procedures like carburizing or nitriding are applied. Surface area firmness reaches 58-62 HRC. Core sturdiness continues to be high. This protects against wear in time.
Accuracy machining makes sure limited resistances. Tooth profiles are reduced to ± 0.005 mm accuracy. Reaction is managed listed below 0.1 mm. This ensures constant harmonizing with paired equipments. The high proportion (generally 3:1 to 5:1) enables speed reduction without sacrificing torque. It suits tools needing high rotational force.
The equipment’s spiral angle ranges between 25-35 degrees. This optimizes tons distribution throughout teeth. Surface ending up consists of grinding or brightening. Rubbing between moving components is lowered. Lubrication periods are prolonged. Upkeep demands are reduced.
Modification choices are offered. Equipment dimension can be changed based upon tool specs. Usual external sizes vary from 20 mm to 150 mm. Bore dimensions match conventional motor shafts. Keyways or set screws secure the equipment in position. Special coatings like zinc plating or black oxide include added defense.
Quality checks follow ISO 1328 requirements. Each equipment undertakes dimensional evaluation. Surface area solidity is checked. Tons capability is verified making use of torque simulation. Sets are labelled with traceability codes. Defects are removed prior to shipping.
Technical assistance aids with installment or pairing. Compatibility charts simplify gear choice. Replacement components are equipped for usual versions. Lead times for customized orders remain under two weeks. Product packaging makes use of anti-rust paper and shock-absorbent foam. Damages throughout transportation is protected against.
(CNC Machined High Ration Spiral Bevel Gear For Power Tool)
Applications of CNC Machined High Ration Spiral Bevel Gear For Power Tool
CNC machined high-ratio spiral bevel equipments are essential components in contemporary power devices. These gears transfer activity in between converging shafts at high angles. Their spiral tooth style makes sure smooth interaction. This decreases resonance and sound during operation. Power tools demand high torque and accuracy. CNC machining accomplishes tight resistances and consistent equipment geometry. This improves efficiency under hefty tons.
High-ratio gearing permits portable device layouts without giving up power. Drills, mills, and saws take advantage of this room effectiveness. The gears handle high rotational rates. Heat generation is decreased through specific tooth get in touch with. This expands the life-span of both gears and tools.
Longevity matters in industrial settings. CNC-machined gears utilize set steel or aerospace-grade alloys. These materials resist wear and contortion. Lubrication retention is boosted by surface area coatings. Maintenance periods end up being longer. Downtime reduces.
Efficiency impacts battery-powered tools. Lower friction in spiral bevel gears decreases energy loss. Battery runtime enhances. Users function longer without reenergizing. Constant power distribution stops electric motor strain. Overheating threats drop.
Personalization is feasible with CNC modern technology. Gear proportions and dimensions adjust to certain tool demands. Prototyping cycles reduce. Producers evaluate layouts much faster. Production scales successfully.
Power devices face varied workloads. Spiral bevel equipments manage sudden load adjustments. Shock absorption avoids tooth damage. Dependability increases popular applications. Automotive repair service, building and construction, and metalworking sectors rely on this effectiveness.
Accuracy placement is crucial. CNC equipments make certain exact gear meshing. Noise degrees stay reduced. Customer convenience boosts during long term use. Smooth operation decreases operator fatigue.
Cost-effectiveness expands over time. High-quality gears reduce replacement frequency. Device long life offsets first expenses. Brands gain credibilities for integrity.
Material option influences performance. Designers pick metals based on application anxieties. Corrosion-resistant coatings secure equipments in extreme conditions. Performance continues to be steady in moist or dusty environments.
CNC machining sustains complicated geometries. Distinct tooth profiles optimize load circulation. Tension concentrations stay clear of powerlessness. Gear failure rates decrease.
Power device technology drives equipment developments. Higher ratios enable smaller sized electric motors with equal output. Portability rises. User control improves. These gears continue to be central to advancing tool layouts.
Campony Introduction
Established in 2002, Shift Gear Machinery Co.,ltd. focus on metal research and mining machinery spare parts. 2 factories over an area of 13,300 square meters, based on 100+ sets of equipment, our production capacity reaches 12000 Tons/Year. has passed ISO 9001 quality managment system certification in 2008.
Our mainly products are dragline excavator spare parts,rotary kiln spare parts, large modulus gear (gear shaft), gearbox ect. 40+ patents with over 45 years experience to help focus on improve the service life of spare parts. We belive that more than 80% reason of mechanical parts’ working life depends on hot processing (steel making/forging/casting/welding/heat treatment). Eight material engineers will control the quality from the original resource.
If you are interested, please feel free to contact us.
Payment
L/C, T/T, Western Union, Paypal, Credit Card etc.
Shipment
By sea, by air, by express, as customers request.
5 FAQs of CNC Machined High Ration Spiral Bevel Gear For Power Tool
What are CNC machined high-ratio spiral bevel gears used for? These gears transfer power between rotating shafts at right angles. They handle high torque and speed in power tools like drills, grinders, or saws. The spiral design reduces noise and vibration. This makes tools last longer and perform better.
Why choose CNC machining for these gears? CNC machines make precise, repeatable cuts. This ensures gears fit perfectly. Tight tolerances mean less wear over time. High-ratio designs need exact tooth profiles. CNC machining achieves this. Manual methods struggle to match this accuracy.
What materials work best for these gears? Steel alloys like 4140 or 8620 are common. They balance strength and wear resistance. Stainless steel is used for corrosion-prone environments. Aluminum suits lightweight tools but handles less load. Material choice depends on tool requirements. Hardness and heat treatment matter for durability.
How do these gears improve power tool performance? High ratios increase torque output. This helps tools cut through tough materials. Spiral teeth engage smoothly. This reduces sudden load changes. Tools run quieter and cooler. Efficiency stays high under heavy use. Less energy is wasted as heat or noise.
Can these gears be customized for specific tools? Yes. Gears are tailored to fit tool size, power, and use cases. Tooth count, angle, and spiral direction are adjustable. Custom ratios match speed and torque needs. Manufacturers provide specs like bore size or mounting details. Compatibility checks ensure gears work with existing systems.
What maintenance do these gears require? Regular lubrication prevents friction and overheating. Grease or oil types depend on operating speeds. Inspect teeth for wear or damage periodically. Replace gears if pitting or chipping appears. Clean debris to avoid contamination. Proper care extends gear life significantly.
(CNC Machined High Ration Spiral Bevel Gear For Power Tool)
REQUEST A QUOTE
RELATED PRODUCTS
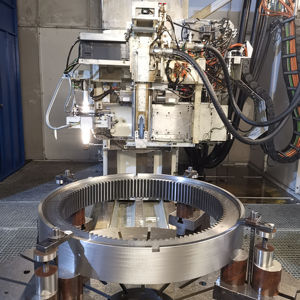
Durable high quality D hole Spur Gear by powder metallurgy

Metallurgy powder customized High precision Stainless Steel Iron bronze Sintered plastic drive gear and spur gear
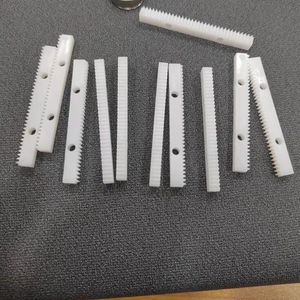
HXMT Spur Gear,Pinion Gear Mod 0.5,0.8,1,1.5,2,etc From China Factory//
JM JK JKL JKD gear reducer driving winch for hoisting pull and unloading tow the weight drop
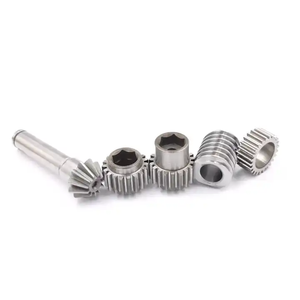
MAR series low backlash and high precision helical gear reducer 60/90/115/142/180 low clearance stepping planetary servo gearbox
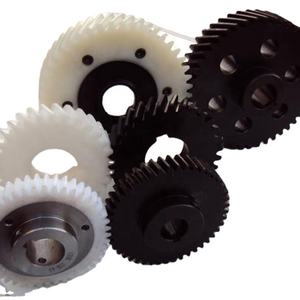