PRODUCT PARAMETERS
Description
Overview of CNC machinery Custom gears High precision Transmission Powder Gear For machine accessories spur gear
Gears are mechanical elements that are typically used to transmit rotational motion and force. They work by meshing teeth with each other to change speed, direction of torque, or to transfer power between multiple shafts. Gears are an integral part of mechanical engineering and are widely used in a variety of mechanical devices.
Advantages and features of CNC machinery Custom gears High precision Transmission Powder Gear For machine accessories spur gear
Efficient transmission: Gears are capable of directly converting power with high efficiency and low energy loss.
Precise ratios: the desired ratio of speed and torque can be obtained by selecting gears of different sizes.
Compact: CNC machinery Custom gears High precision Transmission Powder Gear For machine accessories spur gearsystems take up less space than other forms of power transmission.
High durability: well-designed gears can operate stably for long periods of time in harsh environments.
Low noise and vibration: Modern CNC machinery Custom gears High precision Transmission Powder Gear For machine accessories spur gearmanufacturing technology ensures smooth operation and reduces noise and vibration.
Various types: Spur, helical, and bevel gears are available depending on the application scenario.
(CNC machinery Custom gears High precision Transmission Powder Gear For machine accessories spur gear)
Specifications of CNC machinery Custom gears High precision Transmission Powder Gear For machine accessories spur gear
CNC machinery custom gears deliver high precision for industrial applications. These gears handle transmission systems requiring tight tolerances and reliable performance. Made from high-grade materials like hardened steel or specialized powder metals, they ensure durability under heavy loads. The production process uses advanced CNC machining to achieve accuracy within +/-0.005mm. This level of precision reduces friction, minimizes wear, and extends gear lifespan.
Spur gears from this line feature straightforward tooth profiles. They suit machine accessories needing efficient power transfer without angular complexity. Tooth dimensions are customizable to match specific torque and speed requirements. Common pressure angles include 20° or 25°, balancing smooth operation and load capacity. Surface finishes range from standard milling to polished options for reduced noise in high-speed setups.
Powder metallurgy gears offer unique advantages. The process compacts metal powder into near-net shapes before sintering. This method creates components with uniform density and minimal material waste. Post-machining refines critical surfaces like tooth flanks and bore holes. The result is gears with consistent performance in automotive, robotics, or industrial machinery.
Customization covers gear diameter, bore size, tooth count, and hub configurations. Diameters start at 10mm for small-scale devices and exceed 500mm for heavy machinery. Bore sizes adapt to shafts from 5mm to 200mm. Teeth counts vary between 12 and 120, depending on application needs. Heat treatment options like carburizing or induction hardening enhance surface hardness.
Quality control includes coordinate measuring machines (CMM) and gear testers. These tools verify dimensional accuracy, tooth alignment, and surface integrity. Batch testing ensures compliance with ISO or AGMA standards. Custom packaging solutions protect gears during shipping. Anti-rust coatings or vacuum sealing are available for long-term storage.
These gears integrate into systems requiring exact motion control. Examples include conveyor belts, CNC lathes, and precision actuators. Their design prioritizes easy installation and compatibility with existing setups. Maintenance needs are low due to robust construction and precision manufacturing. Custom orders accommodate small batches or large-scale production runs. Lead times depend on complexity, with standard designs shipping within 7-10 days.
Material certifications and test reports accompany every shipment. Technical support assists with gear selection, load calculations, and integration troubleshooting. Replacement parts maintain the same specifications as original components.
(CNC machinery Custom gears High precision Transmission Powder Gear For machine accessories spur gear)
Applications of CNC machinery Custom gears High precision Transmission Powder Gear For machine accessories spur gear
CNC machinery plays a critical role in manufacturing custom gears for various industries. These machines produce parts with exact measurements. High-precision transmission powder gears are a common application. These gears are used in automotive systems, aerospace equipment, and robotics. CNC technology ensures tight tolerances. This is vital for gears handling heavy loads or high speeds. Powder metallurgy is often combined with CNC machining. Metal powder is compressed and sintered before final shaping. This method reduces material waste. It also improves gear durability. The result is components that perform reliably under stress.
Spur gears for machine accessories are another key product. These gears have straight teeth and a simple design. They transfer motion between parallel shafts efficiently. CNC machines craft these gears from metals like steel or brass. Plastic variants are also possible. The process guarantees smooth operation and long service life. Industries like automotive manufacturing rely on spur gears for transmissions and engines. Industrial machinery uses them for conveyor systems and pumps. Customization is a major advantage. CNC programming adjusts gear size, tooth shape, and material quickly. This flexibility meets specific customer needs.
High-precision gears require flawless surfaces. CNC milling and grinding achieve this. Automated tools reduce human error. Consistency is maintained across large production runs. Complex geometries are handled with ease. This is crucial for specialized applications. Custom gear solutions support innovation in sectors like renewable energy. Wind turbines and solar trackers use CNC-machined gears for precise movement. Medical devices benefit from miniaturized gears made with CNC accuracy.
The ability to work with diverse materials expands CNC’s usefulness. Metals, plastics, and composites are all viable. Engineers test prototypes rapidly using CNC systems. Adjustments are made digitally. This speeds up development cycles. Cost-effective production scales from small batches to mass output. Dependable performance is ensured in every gear produced. CNC machinery remains essential for modern manufacturing demands.
Campony Introduction
Established in 2002, Shift Gear Machinery Co.,ltd. focus on metal research and mining machinery spare parts. 2 factories over an area of 13,300 square meters, based on 100+ sets of equipment, our production capacity reaches 12000 Tons/Year. has passed ISO 9001 quality managment system certification in 2008.
Our mainly products are dragline excavator spare parts,rotary kiln spare parts, large modulus gear (gear shaft), gearbox ect. 40+ patents with over 45 years experience to help focus on improve the service life of spare parts. We belive that more than 80% reason of mechanical parts’ working life depends on hot processing (steel making/forging/casting/welding/heat treatment). Eight material engineers will control the quality from the original resource.
If you are interested, please feel free to contact us.
Payment
L/C, T/T, Western Union, Paypal, Credit Card etc.
Shipment
By sea, by air, by express, as customers request.
5 FAQs of CNC machinery Custom gears High precision Transmission Powder Gear For machine accessories spur gear
What materials are used for custom CNC gears? Common materials include steel, stainless steel, brass, and engineering plastics. These materials are strong, wear-resistant, and handle high stress. The choice depends on the application. Steel suits heavy loads. Stainless steel resists corrosion. Brass works for low-noise environments. Plastics reduce weight and cost.
How precise are CNC custom gears? CNC machining achieves tight tolerances, often within +/- 0.005 mm. Computer-controlled tools follow exact designs, minimizing errors. This precision ensures smooth meshing with other components. It reduces friction and wear. High accuracy is critical for applications like robotics or medical devices.
Can these gears handle high transmission loads? Yes. They are designed for heavy loads. Tooth profiles are optimized for even force distribution. Heat treatment increases hardness and durability. Steel gears handle extreme stress. Proper design prevents tooth breakage. These gears are used in industrial machinery and automotive systems.
What industries use custom powder metal spur gears? Automotive, aerospace, robotics, and manufacturing industries rely on them. Automotive applications include transmissions and engines. Aerospace uses them in landing gear systems. Robotics needs precise motion control. Factories use them in conveyor systems and heavy equipment. Custom gears meet specific operational demands.
How do I maintain CNC-machined spur gears? Regular lubrication reduces friction and heat. Inspect gears for wear or damage. Replace worn parts to avoid system failure. Ensure proper alignment during installation. Clean gears to prevent debris buildup. Maintenance extends gear life and maintains performance. Follow manufacturer guidelines for specific care routines.
(CNC machinery Custom gears High precision Transmission Powder Gear For machine accessories spur gear)
REQUEST A QUOTE
RELATED PRODUCTS
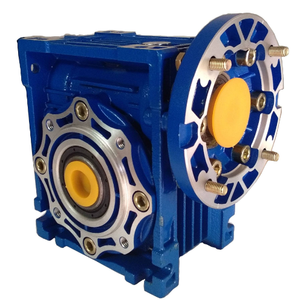
TILI TVB Close Loop Stepper Right Angle 90 Degree Flange Servo Motor Speed Reducer Nema23 Nema34 Nema42 Planetary Gearbox
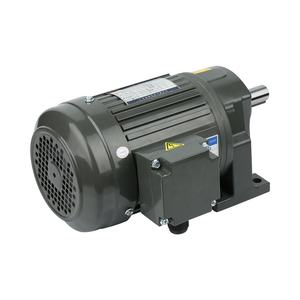
Aokman Solid Shaft Output Cyclo Gear Motor Cycloidal Gearbox for Power Industrial Transmission

B Series bevel-helical High Power 3 stage Gear Speed Reducer Gearbox for Wind Turbine Generator
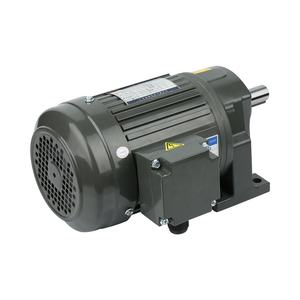
Powder Metallurgy Gears Metal & Metallurgy Machinery Parts
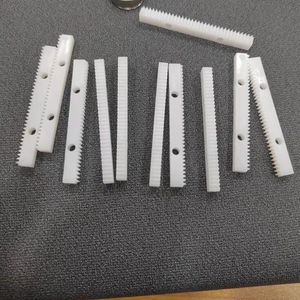