PRODUCT PARAMETERS
Description
Overview of Conic Helical Bevel Gear Pinion Custom Made Helical Gear
Gears are mechanical elements that are typically used to transmit rotational motion and force. They work by meshing teeth with each other to change speed, direction of torque, or to transfer power between multiple shafts. Gears are an integral part of mechanical engineering and are widely used in a variety of mechanical devices.
Advantages and features of Conic Helical Bevel Gear Pinion Custom Made Helical Gear
Efficient transmission: Gears are capable of directly converting power with high efficiency and low energy loss.
Precise ratios: the desired ratio of speed and torque can be obtained by selecting gears of different sizes.
Compact: Conic Helical Bevel Gear Pinion Custom Made Helical Gearsystems take up less space than other forms of power transmission.
High durability: well-designed gears can operate stably for long periods of time in harsh environments.
Low noise and vibration: Modern Conic Helical Bevel Gear Pinion Custom Made Helical Gearmanufacturing technology ensures smooth operation and reduces noise and vibration.
Various types: Spur, helical, and bevel gears are available depending on the application scenario.
(Conic Helical Bevel Gear Pinion Custom Made Helical Gear)
Specifications of Conic Helical Bevel Gear Pinion Custom Made Helical Gear
Our custom-made Conic Helical Bevel Gear Pinion delivers precision-engineered performance for industrial applications. The gear is crafted from high-strength steel alloys such as 20CrMnTi or 42CrMo. These materials ensure durability under heavy loads. Heat treatment processes like carburizing and quenching enhance surface hardness. The core remains tough to resist impact. Teeth profiles are machined using advanced CNC technology. This guarantees accuracy in every tooth angle and curvature. The conic helical design allows smooth power transmission between intersecting shafts. It reduces friction and wear during operation.
The spiral teeth arrangement ensures gradual contact between meshing gears. This minimizes noise and vibration. Load distribution becomes even across the gear surface. The custom design adapts to specific torque and speed requirements. Modules range from 2 to 10. Diameters vary up to 1000mm. Shaft configurations include hollow or solid options. Custom keyways or splines are available for secure mounting.
Precision grinding achieves tooth surface finishes below Ra 0.8μm. This lowers friction and boosts efficiency. Tight tolerance control follows AGMA 2000 or DIN 3961 standards. Backlash is adjustable to suit operational needs. The gears work in angles from 0° to 90°. They handle rotational speeds up to 3000 RPM. Dynamic load ratings reach 5000 Nm. Static load capacities exceed 8000 Nm.
Surface treatments like phosphating or coating prevent rust and corrosion. These gears perform in harsh environments. Options include oil-impregnated or dry lubrication systems. Custom tooth modifications correct alignment issues. This extends service life. The gears integrate with existing machinery. They fit gearboxes, reducers, or power transmission systems.
Applications cover automotive differentials, mining equipment, and wind turbines. High-precision sectors like aerospace use these gears. The design supports bidirectional rotation. It maintains efficiency under fluctuating loads. Testing includes noise level checks and load endurance trials. Each gear undergoes quality certification per ISO 9001 standards. Technical drawings and 3D models are provided for seamless integration. Custom packaging ensures damage-free shipping. Lead times vary based on complexity. Samples are available for performance verification.
(Conic Helical Bevel Gear Pinion Custom Made Helical Gear)
Applications of Conic Helical Bevel Gear Pinion Custom Made Helical Gear
Conic helical bevel gear pinions are specialized mechanical components designed for transmitting power between intersecting shafts at specific angles. Their unique shape combines helical and bevel gear features, enabling smooth torque transfer with high efficiency. Custom-made versions adapt to exact operational requirements, ensuring optimal performance in complex machinery. These gears excel in applications demanding precision, durability, and minimal noise.
Automotive systems use them in differentials and steering mechanisms. The helical teeth reduce vibration, improving vehicle handling and passenger comfort. High load capacity ensures reliability under stress. Aerospace industries rely on these gears for aircraft landing gear systems and engine components. Their ability to handle sudden shifts in force and direction is critical for safety.
Industrial machinery integrates custom helical bevel gears for heavy-duty tasks. Conveyor systems, crushers, and mixers benefit from their resistance to wear and tear. The angled teeth distribute pressure evenly, extending equipment lifespan. Manufacturers customize gear dimensions, materials, and tooth profiles to match specific machine designs.
Renewable energy systems like wind turbines use these gears to transfer rotational energy from blades to generators. Their efficiency in converting motion at varying angles supports stable power output. Custom designs account for environmental factors like temperature changes and moisture.
Robotics and automation employ helical bevel gears for precise motion control. The helical angle allows gradual tooth engagement, reducing backlash. This precision is vital for robotic arms and CNC machines requiring accurate positioning.
Materials like hardened steel, stainless steel, or titanium are chosen based on application needs. Heat treatment and surface finishing enhance strength and corrosion resistance. Each gear undergoes rigorous testing to ensure it meets performance standards.
Customization options include modifications to helix angles, pitch diameters, and gear ratios. Engineers work closely with clients to address unique challenges, such as space constraints or unusual operating conditions. This flexibility makes conic helical bevel gears suitable for both standard and niche applications.
The combination of advanced manufacturing techniques and tailored design ensures these gears deliver consistent performance. They reduce energy loss, lower maintenance costs, and improve system reliability across industries.
Campony Introduction
Established in 2002, Shift Gear Machinery Co.,ltd. focus on metal research and mining machinery spare parts. 2 factories over an area of 13,300 square meters, based on 100+ sets of equipment, our production capacity reaches 12000 Tons/Year. has passed ISO 9001 quality managment system certification in 2008.
Our mainly products are dragline excavator spare parts,rotary kiln spare parts, large modulus gear (gear shaft), gearbox ect. 40+ patents with over 45 years experience to help focus on improve the service life of spare parts. We belive that more than 80% reason of mechanical parts’ working life depends on hot processing (steel making/forging/casting/welding/heat treatment). Eight material engineers will control the quality from the original resource.
If you are interested, please feel free to contact us.
Payment
L/C, T/T, Western Union, Paypal, Credit Card etc.
Shipment
By sea, by air, by express, as customers request.
5 FAQs of Conic Helical Bevel Gear Pinion Custom Made Helical Gear
A conic helical bevel gear pinion transfers motion between intersecting shafts. The teeth align at an angle. This design reduces noise. It handles heavy loads smoothly. Custom versions fit exact machine requirements. These gears suit setups needing precision torque control.
These gears work in mining equipment. They operate in automotive systems. Heavy machinery uses them for power transmission. High-load applications rely on their durability. They perform well in tight spaces. Industries choose them for efficiency under stress.
Customization covers gear size. Tooth count adjusts to match gear ratios. Material selection depends on load capacity. Helix angles change based on alignment needs. Surface treatments improve wear resistance. Engineers tweak designs for specific operating conditions.
Common materials include carbon steel. Alloy steel offers higher strength. Stainless steel resists corrosion. Case hardening increases surface durability. Heat-treated gears last longer under stress. Material choice balances cost and performance.
Gear lifespan varies. Proper installation extends service life. Regular lubrication prevents premature wear. Load limits affect durability. Harsh environments reduce longevity. High-quality materials and correct maintenance ensure years of reliable operation.
(Conic Helical Bevel Gear Pinion Custom Made Helical Gear)
REQUEST A QUOTE
RELATED PRODUCTS
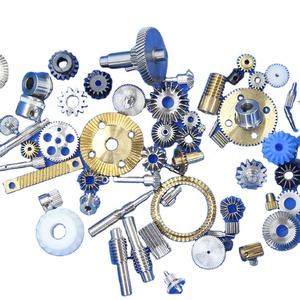
Precision Worm Gear And Shaft Made In China Gear Wheel Straight Tooth Gear Worm Wheel,Worm Gear,Gear Worm Gear
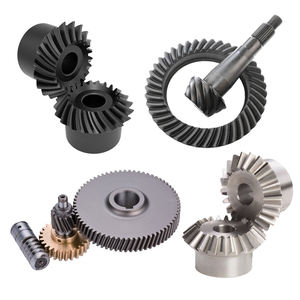
Cnc Precision Machining Service Titanium Cnc Machining Milling Turning Gear Parts

OEM Factory in China Micro Machining CNC Machining Parts Stainless Steel Spiral Bevel Gear for Drilling and Rapid Prototyping

High Precision Custom 45 Steel Spline Hub Sleeve Parts Power Transmission Spur Gears Helical Gears Bevel Gears
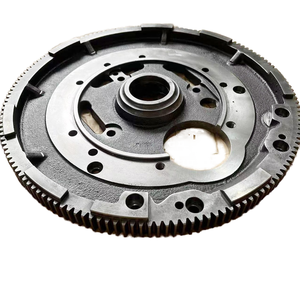
Custom MOD. 1.0 1.5 2 2.5 3 4 5 Drive Big Helical Gear Spur Pinion Gear Wheel Herringbone Gear
