PRODUCT PARAMETERS
Description
Overview of Custom Precision Machining Precision Engineered Gear Solutions Tailored Gear Products to Meet Your Unique Demands
Gears are mechanical elements that are typically used to transmit rotational motion and force. They work by meshing teeth with each other to change speed, direction of torque, or to transfer power between multiple shafts. Gears are an integral part of mechanical engineering and are widely used in a variety of mechanical devices.
Advantages and features of Custom Precision Machining Precision Engineered Gear Solutions Tailored Gear Products to Meet Your Unique Demands
Efficient transmission: Gears are capable of directly converting power with high efficiency and low energy loss.
Precise ratios: the desired ratio of speed and torque can be obtained by selecting gears of different sizes.
Compact: Custom Precision Machining Precision Engineered Gear Solutions Tailored Gear Products to Meet Your Unique Demandssystems take up less space than other forms of power transmission.
High durability: well-designed gears can operate stably for long periods of time in harsh environments.
Low noise and vibration: Modern Custom Precision Machining Precision Engineered Gear Solutions Tailored Gear Products to Meet Your Unique Demandsmanufacturing technology ensures smooth operation and reduces noise and vibration.
Various types: Spur, helical, and bevel gears are available depending on the application scenario.
(Custom Precision Machining Precision Engineered Gear Solutions Tailored Gear Products to Meet Your Unique Demands)
Specifications of Custom Precision Machining Precision Engineered Gear Solutions Tailored Gear Products to Meet Your Unique Demands
Custom Precision Machining delivers high-performance, precision-engineered gear solutions tailored to meet the exacting demands of diverse industries. Our custom gear products are designed with advanced engineering principles, leveraging state-of-the-art CNC machining, gear hobbing, grinding, and shaping technologies to ensure unmatched accuracy and reliability. We specialize in producing spur gears, helical gears, bevel gears, worm gears, planetary gears, and custom gear assemblies, all crafted to your unique specifications. Materials range from high-strength alloys like stainless steel, aluminum, brass, and titanium to engineered plastics, ensuring optimal performance in applications requiring corrosion resistance, lightweight design, or extreme durability.
Every gear is manufactured to tight tolerances, often achieving AGMA Q10 or ISO 1328 Class 6-8 standards, with surface finishes as low as Ra 0.4μm for reduced friction and noise. Our processes include heat treatment, carburizing, nitriding, and coatings like TiN or DLC to enhance wear resistance and lifespan. Customization extends to tooth profiles, pressure angles, module sizes, and bore configurations, ensuring seamless integration into your systems.
Quality assurance is integral to our workflow, with 3D modeling, Finite Element Analysis (FEA), and rigorous inspection via CMMs, optical comparators, and backlash testers. We comply with ISO 9001:2015 and AS9100D standards, guaranteeing traceability and consistency. Whether you need prototypes for testing or high-volume production, our scalable solutions cater to industries such as automotive, aerospace, robotics, renewable energy, and heavy machinery.
Collaborate with our engineering team to optimize gear designs for load capacity, efficiency, noise reduction, or space constraints. From concept to delivery, we prioritize rapid turnaround without compromising precision. Our gears empower applications like powertrains, robotics actuation, wind turbines, and medical devices, where performance and reliability are non-negotiable. Trust Custom Precision Machining for gears engineered to excel in the most demanding environments, backed by technical expertise and a commitment to exceeding your expectations.
(Custom Precision Machining Precision Engineered Gear Solutions Tailored Gear Products to Meet Your Unique Demands)
Applications of Custom Precision Machining Precision Engineered Gear Solutions Tailored Gear Products to Meet Your Unique Demands
Custom precision machining is revolutionizing industries by delivering high-performance gear solutions engineered to meet the most demanding specifications. Precision engineered gears are critical components in applications where accuracy, durability, and efficiency are non-negotiable. From aerospace and automotive systems to robotics, medical devices, and renewable energy technology, custom gears ensure seamless power transmission, reduced wear, and optimized performance. Tailored gear products address unique challenges across sectors, offering solutions that standard off-the-shelf components simply cannot match. In aerospace, custom gears enable lightweight yet robust designs for aircraft engines and landing systems, ensuring reliability under extreme conditions. Automotive manufacturers rely on precision-machined gears for electric vehicle drivetrains, transmission systems, and steering mechanisms, prioritizing noise reduction and energy efficiency. Robotics and automation demand ultra-precise gears for motion control, enabling speed, accuracy, and repeatability in manufacturing and assembly lines. The medical industry benefits from miniature gears used in surgical tools and imaging devices, where biocompatible materials and micron-level tolerances are essential. Heavy machinery and renewable energy systems, such as wind turbines, depend on custom gears to handle high torque and variable loads while minimizing downtime. Custom precision machining allows for flexibility in material selection, including steel, titanium, brass, and advanced composites, paired with specialized coatings to enhance corrosion resistance and longevity. Advanced techniques like CNC machining, gear hobbing, grinding, and 3D printing ensure exacting standards for tooth profiles, surface finishes, and load capacities. By collaborating with engineers, businesses can develop gears tailored to their exact operational requirements, whether modifying existing designs or innovating new solutions. Beyond performance, custom gears reduce long-term costs by extending equipment lifespans and minimizing maintenance. Quality assurance through rigorous testing, including stress analysis and dimensional inspection, guarantees compliance with industry certifications. Partnering with a precision machining expert ensures access to cutting-edge technology and technical support, from prototyping to full-scale production. Whether enhancing efficiency, solving unique engineering challenges, or driving innovation, custom precision-engineered gear solutions empower industries to achieve their goals with unmatched reliability and precision.
Campony Introduction
Established in 2002, Shift Gear Machinery Co.,ltd. focus on metal research and mining machinery spare parts. 2 factories over an area of 13,300 square meters, based on 100+ sets of equipment, our production capacity reaches 12000 Tons/Year. has passed ISO 9001 quality managment system certification in 2008.
Our mainly products are dragline excavator spare parts,rotary kiln spare parts, large modulus gear (gear shaft), gearbox ect. 40+ patents with over 45 years experience to help focus on improve the service life of spare parts. We belive that more than 80% reason of mechanical parts’ working life depends on hot processing (steel making/forging/casting/welding/heat treatment). Eight material engineers will control the quality from the original resource.
If you are interested, please feel free to contact us.
Payment
L/C, T/T, Western Union, Paypal, Credit Card etc.
Shipment
By sea, by air, by express, as customers request.
5 FAQs of Custom Precision Machining Precision Engineered Gear Solutions Tailored Gear Products to Meet Your Unique Demands
Custom precision machining for gears involves advanced manufacturing techniques to create highly accurate, tailor-made gear components that meet specific application requirements. This process utilizes state-of-the-art CNC machines, grinding equipment, and quality control systems to produce gears with exact tolerances, unique geometries, or specialized materials. It is ideal for industries like aerospace, automotive, robotics, and industrial machinery where off-the-shelf gears cannot meet performance, durability, or size demands.
Why should I choose custom gears over standard options? Custom gears are designed to address challenges that standard gears cannot, such as unusual load capacities, extreme operating environments, or space constraints. They ensure optimal performance by aligning with your exact torque, speed, noise reduction, and efficiency needs. Custom solutions also future-proof your operations by adapting to evolving technological demands or proprietary designs, reducing long-term maintenance costs and downtime.
What materials are commonly used in precision-engineered gears? High-grade steels (like 4140 or 4340), stainless steel, aluminum, brass, and thermoplastics are typical choices. For extreme conditions, materials such as titanium, nickel alloys, or ceramic-coated metals may be used. The selection depends on factors like weight, corrosion resistance, thermal stability, and wear resistance. Engineers work with you to determine the best material based on your application’s stress levels, environment, and lifecycle expectations.
What is the typical lead time for custom gear production? Lead times vary based on design complexity, material availability, and order volume. Simple designs may take 2–4 weeks, while highly complex projects could require 8–12 weeks. Reputable manufacturers prioritize transparent timelines and employ agile workflows to expedite production without compromising quality. Rush services are often available for urgent projects.
How do you ensure the quality of custom gears? Quality is maintained through rigorous inspections at every stage, from material certification to final assembly. Advanced tools like coordinate measuring machines (CMM), optical comparators, and hardness testers verify dimensional accuracy and material integrity. Many providers adhere to ISO 9001 or AS9100 standards and offer traceable documentation. Post-production testing, such as load endurance or noise-vibration-harshness (NVH) analysis, ensures gears perform as specified in real-world conditions.
By focusing on precision, customization, and rigorous quality control, custom gear machining delivers solutions that enhance performance, efficiency, and reliability for your unique applications. Partnering with an experienced manufacturer ensures seamless integration into your systems, reducing risk and maximizing ROI.
(Custom Precision Machining Precision Engineered Gear Solutions Tailored Gear Products to Meet Your Unique Demands)
REQUEST A QUOTE
RELATED PRODUCTS
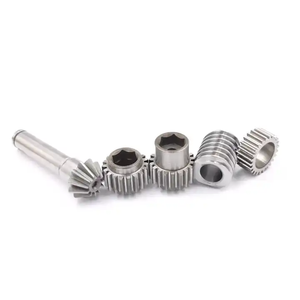
CHENGGANG 0.2KW small reduction gearbox motor Horizontal Asynchronous Motor with brake AC motor with reducer
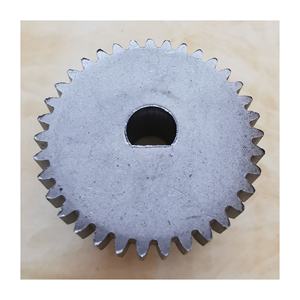
High Precision Custom Size Nylon POM Small Swing Gear For Machines

Chinese Factory 10T Mechanical skid-resistant gear puller
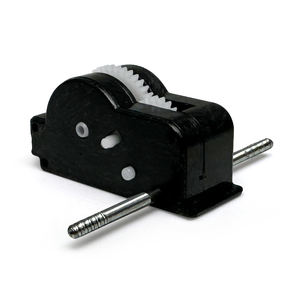
YK3608 High Efficiency Horizontal CNC Gear Hobbing Machine For Mini Gear Cutter Machine
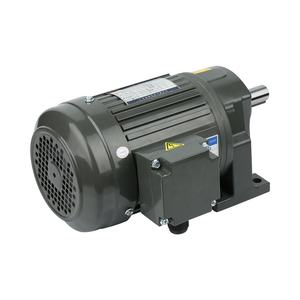
s High Precision Cnc Milling Turning Service Steel Bevel Gears Custom Spur Gears Sets
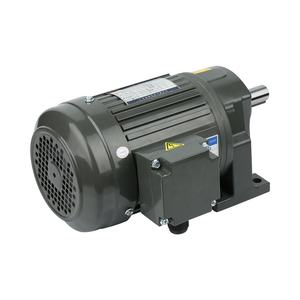