PRODUCT PARAMETERS
Description
Overview of Customized Non-Standard Helical Gear for Transmission System Precision Casting Steel Gearbox Core Components
Gears are mechanical elements that are typically used to transmit rotational motion and force. They work by meshing teeth with each other to change speed, direction of torque, or to transfer power between multiple shafts. Gears are an integral part of mechanical engineering and are widely used in a variety of mechanical devices.
Advantages and features of Customized Non-Standard Helical Gear for Transmission System Precision Casting Steel Gearbox Core Components
Efficient transmission: Gears are capable of directly converting power with high efficiency and low energy loss.
Precise ratios: the desired ratio of speed and torque can be obtained by selecting gears of different sizes.
Compact: Customized Non-Standard Helical Gear for Transmission System Precision Casting Steel Gearbox Core Componentssystems take up less space than other forms of power transmission.
High durability: well-designed gears can operate stably for long periods of time in harsh environments.
Low noise and vibration: Modern Customized Non-Standard Helical Gear for Transmission System Precision Casting Steel Gearbox Core Componentsmanufacturing technology ensures smooth operation and reduces noise and vibration.
Various types: Spur, helical, and bevel gears are available depending on the application scenario.
(Customized Non-Standard Helical Gear for Transmission System Precision Casting Steel Gearbox Core Components)
Specifications of Customized Non-Standard Helical Gear for Transmission System Precision Casting Steel Gearbox Core Components
Customized non-standard helical gears are designed for precision casting steel gearbox core components in transmission systems. These gears meet specific operational needs in industrial applications. Made from high-grade steel alloys, they ensure durability under heavy loads and high-speed conditions. The manufacturing process focuses on precision casting to achieve accurate tooth profiles and minimal distortion. This guarantees smooth power transfer and reduces wear over time.
The gears are customizable in size, shape, tooth profile, and helix angle. Adjustments are made to fit unique mechanical setups or match existing systems. Options include modules from 1 to 10, diameters from 20mm to 2000mm, and teeth counts between 15 and 150. Pressure angles can be modified to optimize contact ratios. Surface treatments like carburizing or nitriding enhance hardness and corrosion resistance.
Tight tolerances (IT6-IT8) are maintained through advanced machining and quality control. This ensures seamless integration with gearbox assemblies. Heat treatment processes improve core strength, achieving hardness levels of HRC 58-62. The helical design reduces noise and vibration during operation. It also increases load distribution across gear teeth, boosting efficiency in high-torque environments.
Each gear undergoes rigorous testing. Dimensional accuracy is verified using coordinate measuring machines. Hardness is tested with Rockwell or Vickers methods. Load capacity is assessed through fatigue and stress tests. Material composition is checked via spectral analysis to confirm alloy integrity.
These gears are used in automotive transmissions, industrial machinery, mining equipment, and renewable energy systems. They handle demanding applications like heavy-duty gearboxes, conveyor systems, and precision pumps. Customization ensures compatibility with both standard and non-standard gearbox designs. The focus on precision and material quality minimizes downtime and maintenance costs.
Surface finishes are tailored to reduce friction. Grinding or honing achieves roughness levels as low as Ra 0.4μm. Anti-wear coatings like titanium nitride extend service life. Lubrication grooves or holes can be added to improve heat dissipation. Custom packaging is available for safe transport and storage. Technical support is provided for installation and troubleshooting.
(Customized Non-Standard Helical Gear for Transmission System Precision Casting Steel Gearbox Core Components)
Applications of Customized Non-Standard Helical Gear for Transmission System Precision Casting Steel Gearbox Core Components
Customized non-standard helical gears play a key role in transmission systems. These gears are designed for precision casting steel gearbox core components. Their unique shape allows smooth power transfer between rotating shafts. This reduces noise during operation. The angled teeth of helical gears create gradual contact. This design spreads load evenly across the gear surface. It improves durability under heavy use.
Industries requiring high-performance machinery use these gears widely. Automotive manufacturers apply them in advanced drivetrain systems. The gears handle increased torque demands in electric vehicles. Industrial machinery relies on them for conveyor systems. Mining equipment uses these gears for consistent performance in harsh conditions. Aerospace applications benefit from their reliability in critical flight control mechanisms.
Precision casting methods ensure tight tolerances for steel gearbox components. This process creates complex shapes with minimal machining. It maintains material strength while reducing production waste. Customized helical gears fit exact specifications for unique transmission setups. Modifications in tooth angle or helix direction address specific load requirements.
The steel used in these gears undergoes strict quality checks. Heat treatment enhances hardness. Surface finishing reduces friction. Corrosion-resistant coatings extend service life. These steps ensure gears perform in extreme temperatures. They withstand exposure to chemicals.
Customization allows adaptation to space-constrained environments. Compact gearboxes in robotics use tailored helical gears. Wind turbine manufacturers integrate them for efficient energy transfer. Marine propulsion systems depend on their resistance to saltwater damage.
Regular maintenance of these gears prevents unexpected failures. Proper lubrication minimizes wear. Vibration analysis detects alignment issues early. This proactive approach reduces downtime. It extends the lifespan of transmission systems.
The flexibility of non-standard designs solves engineering challenges. Mismatched shaft angles in machinery become manageable. Variable speed applications achieve smoother transitions. Power loss decreases. Operational efficiency rises.
Demand for precision-cast steel gears grows with automation trends. Manufacturers seek components offering reliability. Custom helical gears meet this need. They support innovation across multiple sectors. Their role in modern mechanical systems remains vital.
Campony Introduction
Established in 2002, Shift Gear Machinery Co.,ltd. focus on metal research and mining machinery spare parts. 2 factories over an area of 13,300 square meters, based on 100+ sets of equipment, our production capacity reaches 12000 Tons/Year. has passed ISO 9001 quality managment system certification in 2008.
Our mainly products are dragline excavator spare parts,rotary kiln spare parts, large modulus gear (gear shaft), gearbox ect. 40+ patents with over 45 years experience to help focus on improve the service life of spare parts. We belive that more than 80% reason of mechanical parts’ working life depends on hot processing (steel making/forging/casting/welding/heat treatment). Eight material engineers will control the quality from the original resource.
If you are interested, please feel free to contact us.
Payment
L/C, T/T, Western Union, Paypal, Credit Card etc.
Shipment
By sea, by air, by express, as customers request.
5 FAQs of Customized Non-Standard Helical Gear for Transmission System Precision Casting Steel Gearbox Core Components
Customized non-standard helical gears fit specific transmission systems. Standard gears may not meet unique industrial needs. These gears adapt to exact space, torque, speed requirements. Precision casting steel ensures strength, durability. They suit applications where off-the-shelf solutions fail.
Helical gears reduce noise, handle higher loads better than spur gears. Teeth engage gradually, minimizing sudden contact. This lowers wear, extends gearbox life. Customization tailors helix angles, tooth profiles for optimal performance. Transmission efficiency improves, energy loss decreases.
Custom orders start with detailed client specifications. Engineers analyze load, speed, environmental conditions. CAD software models gear geometry. Adjustments ensure compatibility with existing systems. Prototypes undergo testing. Final designs use precision casting for accuracy. Modifications happen anytime during production.
High-grade steel alloys are common. Carbon steel, chromium-molybdenum steel offer strength, fatigue resistance. Heat treatment enhances surface hardness, core toughness. Corrosion-resistant coatings apply for harsh environments. Material choice depends on operating stress, temperature, exposure to chemicals.
Quality checks happen at every stage. Raw materials get tested for defects. Casting processes follow strict tolerances. Finished gears undergo stress tests, wear analysis. Dimensional accuracy verifies using laser scanners. Real-world simulations mimic operating conditions. Defective parts get rejected immediately. Regular maintenance guidelines help users maximize lifespan.
(Customized Non-Standard Helical Gear for Transmission System Precision Casting Steel Gearbox Core Components)
REQUEST A QUOTE
RELATED PRODUCTS
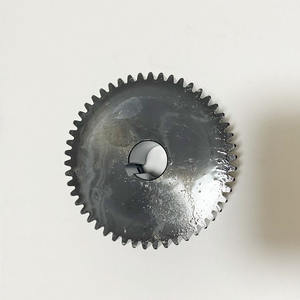
SLTM reduction gear box
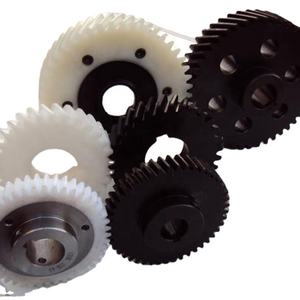
Aluminum Light Weight Gearbox Cast Iron Strong Housing Transmission Drive Reduction Worm Gearboxes Speed Gear Reducer
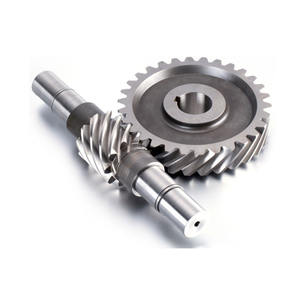
High Accuracy OEM Machining Cnc Milling Transmission Part Oxide Black Stainless Steel Wheel Spur gear

Hot 4140 Alloy Steel Forged Gear Ring For Construction Machinery, Forging Slewing Bearing With CNC Machining For Marine
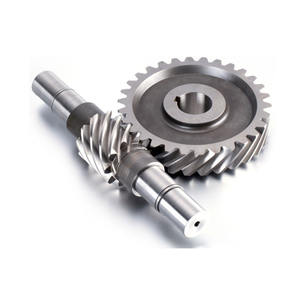