PRODUCT PARAMETERS
Description
Overview of Differential Helical Pinion Gear Units Module 1.25 2 6
Gears are mechanical elements that are typically used to transmit rotational motion and force. They work by meshing teeth with each other to change speed, direction of torque, or to transfer power between multiple shafts. Gears are an integral part of mechanical engineering and are widely used in a variety of mechanical devices.
Advantages and features of Differential Helical Pinion Gear Units Module 1.25 2 6
Efficient transmission: Gears are capable of directly converting power with high efficiency and low energy loss.
Precise ratios: the desired ratio of speed and torque can be obtained by selecting gears of different sizes.
Compact: Differential Helical Pinion Gear Units Module 1.25 2 6systems take up less space than other forms of power transmission.
High durability: well-designed gears can operate stably for long periods of time in harsh environments.
Low noise and vibration: Modern Differential Helical Pinion Gear Units Module 1.25 2 6manufacturing technology ensures smooth operation and reduces noise and vibration.
Various types: Spur, helical, and bevel gears are available depending on the application scenario.
(Differential Helical Pinion Gear Units Module 1.25 2 6)
Specifications of Differential Helical Pinion Gear Units Module 1.25 2 6
Differential helical pinion gear systems module 1.25, 2, and 6 are crafted for precision power transmission in commercial equipment. These units combine helical gear performance with compact style. The helical teeth minimize noise and resonance during procedure. The component sizes deal with different torque and rate requirements.
Module 1.25 fits light-duty applications. It handles torque as much as 50 Nm. The system operates smoothly at quicken to 3000 RPM. The compact size fits space-constrained arrangements. It is perfect for tiny conveyors or product packaging tools. Steel building and construction makes certain longevity. Heat therapy improves wear resistance.
Module 2 balances tool torque and rate. It supports torque approximately 150 Nm. Operating rates get to 2500 RPM. The layout focuses on lots circulation across equipment teeth. This decreases tension and extends life span. Applications consist of mixers or product handling systems. The housing is cast iron for stability. Secured bearings avoid contamination.
Module 6 takes care of sturdy jobs. Torque capability surpasses 600 Nm. Rates stay stable approximately 1500 RPM. Big gear teeth enhance load-bearing capability. This component operates in crushers or heavy conveyors. The housing includes cooling down fins for warmth dissipation. Internal parts use case-hardened steel. Surface grinding makes sure accurate equipment positioning.
All components feature adjustable reaction settings. This enables fine-tuning for smooth operation. Lubrication ports streamline maintenance. Secured housings shield versus dust and dampness. Installing options include flange or base arrangements. Customized shaft sizes are available.
Helical gears offer greater contact proportions than stimulate gears. This enhances efficiency and lowers wear. The differential style allows rate variation in between output shafts. It adapts to unequal tons distribution. Applications benefit from constant performance under variable problems.
Equipment units go through rigorous testing. Examinations consist of tons cycles and thermal checks. Quality assurance makes certain conformity with sector standards. Each system is inspected prior to delivery.
Products are chosen for stamina and longevity. Steel alloys resist contortion under tension. Surface area treatments prevent rust. Seals and gaskets maintain interior cleanliness.
These equipment units incorporate right into existing systems quickly. Installment needs typical tools. Maintenance periods are expanded due to durable building. Technical support is offered for fixing.
Efficiency information is offered each component. This consists of torque curves and performance scores. Users can pick systems based upon specific operational needs.
(Differential Helical Pinion Gear Units Module 1.25 2 6)
Applications of Differential Helical Pinion Gear Units Module 1.25 2 6
Differential helical pinion equipment devices with components 1.25, 2, and 6 are used in several sectors. These equipment devices incorporate helical teeth with a differential configuration. The style enables smooth power transfer and high torque handling. They work well in systems needing exact activity control and compact size. The module dimensions fit different load requirements. Component 1.25 matches lighter tons, module 2 takes care of medium tons, module 6 handles durable applications.
These equipments prevail in making devices. Conveyor systems utilize them for steady product transport. Product packaging equipments count on their accuracy for regular product handling. Production line benefit from their durability under repetitive tasks. Automotive applications include steering systems and transmission setups. The helical teeth lower sound, making them ideal for electrical automobiles. Differential activity improves wheel synchronization in drivetrains.
Robotics is another key location. Robotic arms require exact joint activities. These gears offer the essential control for tasks like welding or setting up. Their compact dimension matches tight rooms within robotic frameworks. Clinical tools utilize them for accurate placing in imaging equipments or surgical tools. The low resonance ensures stable procedure in sensitive settings.
Renewable energy systems use these gear units as well. Wind generators call for trustworthy power transmission from blades to generator. The differential setup deals with speed variations brought on by changing wind problems. Solar tracking systems change panel angles using these equipments for maximum sunshine capture. Their high performance lowers power loss in renewable arrangements.
Hefty machinery depends upon component 6 devices for mining or building devices. Excavators and cranes utilize them for raising and excavating procedures. The equipments withstand shock lots and extreme settings. Agricultural equipment like harvesters utilizes them for power circulation between elements. Longevity ensures lengthy life span despite consistent use.
Personalization options allow these gears adjust to particular needs. Engineers readjust equipment proportions or housing materials for unique applications. This adaptability makes them suitable for aerospace, marine, and commercial automation. The mix of helical and differential designs ensures dependable efficiency throughout industries.
Campony Introduction
Established in 2002, Shift Gear Machinery Co.,ltd. focus on metal research and mining machinery spare parts. 2 factories over an area of 13,300 square meters, based on 100+ sets of equipment, our production capacity reaches 12000 Tons/Year. has passed ISO 9001 quality managment system certification in 2008.
Our mainly products are dragline excavator spare parts,rotary kiln spare parts, large modulus gear (gear shaft), gearbox ect. 40+ patents with over 45 years experience to help focus on improve the service life of spare parts. We belive that more than 80% reason of mechanical parts’ working life depends on hot processing (steel making/forging/casting/welding/heat treatment). Eight material engineers will control the quality from the original resource.
If you are interested, please feel free to contact us.
Payment
L/C, T/T, Western Union, Paypal, Credit Card etc.
Shipment
By sea, by air, by express, as customers request.
5 FAQs of Differential Helical Pinion Gear Units Module 1.25 2 6
Differential Helical Pinion Gear Units Module 1.25 2 6 are mechanical systems designed to transfer torque between non-parallel shafts. Their teeth are angled for smoother engagement. These units come in modules 1.25, 2, and 6. They reduce noise and vibration compared to spur gears. Common uses include industrial machinery and automotive systems.
These gear units suit applications needing precise power transmission. Examples include conveyor systems, packaging machines, and robotics. They work well in automotive differentials. Their design handles high torque loads. They support efficient motion control in tight spaces.
The gears are made from high-strength steel alloys. Case-hardened steel is typical. Heat treatment enhances durability. Materials are chosen for wear resistance. This ensures long service life under heavy loads.
Regular maintenance is necessary. Inspect gears for wear or damage every 3-6 months. Lubricate bearings and teeth surfaces every 1,000 operating hours. Use manufacturer-recommended grease. Keep the unit clean from dust and debris. Check for unusual noises during operation. Address issues immediately to prevent failures.
Helical gears outperform spur gears in multiple ways. Angled teeth reduce impact during engagement. This lowers noise levels. Load distribution across teeth improves. Higher torque capacity is achieved. Efficiency remains stable under varying speeds.
(Differential Helical Pinion Gear Units Module 1.25 2 6)
REQUEST A QUOTE
RELATED PRODUCTS
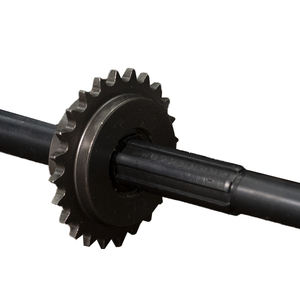
High Hardness 4140 Material Crown Wheel Spiral Bevel Gear for Sewing Machine

HXMT Auto Parts Custom Steel Driving Spur Gear And Foring Bevel Gear Ring Gear From Shenzhen
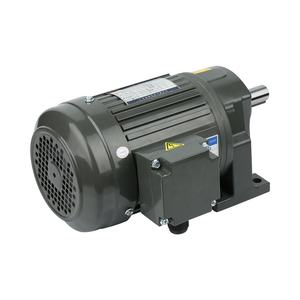
Steel Precision tooth gearbox 60 size 45Nm small backlash 5 arcmin for nema 24 and nema 23 servo stepper bldc motors bevel gear
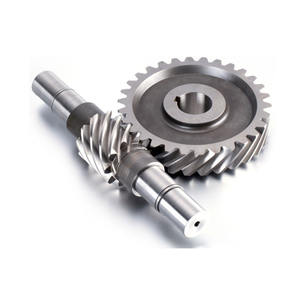
P2L Bevel gear Stage Industrial Gearbox Industrial Planetary Reducer For New Energy Industry
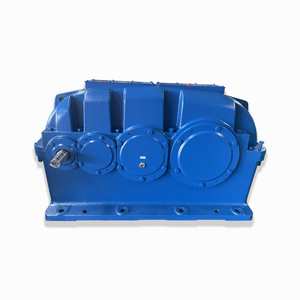