PRODUCT PARAMETERS
Description
Overview of Factory Custom Quality Assurance Smooth Transmission Plastic Gear PP PEEK POM Nylon Gear With High Precision
Gears are mechanical elements that are typically used to transmit rotational motion and force. They work by meshing teeth with each other to change speed, direction of torque, or to transfer power between multiple shafts. Gears are an integral part of mechanical engineering and are widely used in a variety of mechanical devices.
Advantages and features of Factory Custom Quality Assurance Smooth Transmission Plastic Gear PP PEEK POM Nylon Gear With High Precision
Efficient transmission: Gears are capable of directly converting power with high efficiency and low energy loss.
Precise ratios: the desired ratio of speed and torque can be obtained by selecting gears of different sizes.
Compact: Factory Custom Quality Assurance Smooth Transmission Plastic Gear PP PEEK POM Nylon Gear With High Precisionsystems take up less space than other forms of power transmission.
High durability: well-designed gears can operate stably for long periods of time in harsh environments.
Low noise and vibration: Modern Factory Custom Quality Assurance Smooth Transmission Plastic Gear PP PEEK POM Nylon Gear With High Precisionmanufacturing technology ensures smooth operation and reduces noise and vibration.
Various types: Spur, helical, and bevel gears are available depending on the application scenario.
(Factory Custom Quality Assurance Smooth Transmission Plastic Gear PP PEEK POM Nylon Gear With High Precision)
Specifications of Factory Custom Quality Assurance Smooth Transmission Plastic Gear PP PEEK POM Nylon Gear With High Precision
Manufacturing Facility Custom-made Quality Assurance Smooth Transmission Plastic Gear (PP, PEEK, POM, Nylon) with High Precision is engineered for sturdiness, performance, and dependability in demanding applications. These gears are produced using sophisticated polymer materials, consisting of polypropylene (PP), polyether ether ketone (PEEK), polyoxymethylene (POM), and nylon (), making sure optimal performance across varied sectors. Each product offers distinct properties: PP gives chemical resistance and light-weight versatility, PEEK supplies exceptional thermal security (up to 250 ° C )and mechanical stamina, POM guarantees reduced rubbing and high stiffness, while nylon masters wear resistance and load-bearing capacity. Precision-machined to limited resistances ( ± 0.005 mm), these equipments ensure smooth meshing and marginal noise throughout operation. Tooth profiles are maximized making use of CNC machining or shot molding methods to accomplish AGMA or ISO 1328 requirements, making certain accurate power transmission. Surface coatings are brightened to Ra ≤ 0.8 µm for lowered rubbing and enhanced longevity. Birthed sizes array from 2 mm to 200 mm, with alternatives for keyways, set screws, or customized splines. Gears are examined for torque capacity (as much as 50 Nm, relying on product), rotational speed (up to 3000 RPM), and ecological resistance (humidity, chemicals, UV). Quality control consists of 100% dimensional evaluation through CMM, tons screening, and tiredness evaluation to ensure conformity with ISO 9001 standards. Modification is available for equipment modulus (0.5– 5), stress angles (14.5 °– 25 ° ), and helix angles (0 °– 45 °). Applications include vehicle systems, clinical tools, robotics, industrial machinery, and customer electronic devices. All gears are RoHS-compliant and undergo extensive set testing for thermal development, creep resistance, and dimensional security. Optional accreditations (FDA, USP Course VI) are available for medical-grade PEEK or POM equipments. Lead times vary from 2– 6 weeks, with MOQs starting at 100 devices. Custom product packaging, branding, and material accreditations (UL, REACH) are supplied upon demand. These gears are excellent for OEMs seeking high-precision, low-maintenance remedies with lifetime lubrication-free operation in severe problems.
(Factory Custom Quality Assurance Smooth Transmission Plastic Gear PP PEEK POM Nylon Gear With High Precision)
Applications of Factory Custom Quality Assurance Smooth Transmission Plastic Gear PP PEEK POM Nylon Gear With High Precision
Factory-customized plastic equipments made from high-performance products like PP (polypropylene), PEEK (polyetheretherketone), POM (polyoxymethylene/acetal), and nylon are engineered to supply smooth transmission, remarkable precision, and durable longevity. These equipments are developed for sectors needing reliable, lightweight, and corrosion-resistant options where traditional steel gears fail. Their custom quality control procedures ensure each equipment satisfies strict performance criteria, making them suitable for applications demanding high accuracy and marginal maintenance.
** PP Gears **: Polypropylene gears master settings needing chemical resistance and reduced dampness absorption. They are generally utilized in food processing equipment, product packaging equipment, and automotive fluid systems because of their non-toxic, lightweight homes and ability to operate quietly under moderate stress.
** PEEK Equipments **: Recognized for extreme thermal stability (approximately 250 ° C) and mechanical strength, PEEK equipments are essential in aerospace, oil and gas, and clinical gadgets. They withstand high temperatures, aggressive chemicals, and sanitation procedures, making them appropriate for airplane actuators, pump systems, and surgical tool drives.
** POM Gears **: Acetal gears offer reduced rubbing, high stiffness, and exceptional dimensional stability, suitable for precision auto parts (e.g., home window regulatory authorities, seat adjusters), customer electronic devices (printers, cameras), and industrial equipment. Their reduced wear price ensures smooth, regular activity in high-cycle applications.
** Nylon Gears **: Nylon’s high effect resistance and noise-dampening homes make it a top selection for power devices, conveyor systems, and robotics. Glass-reinforced nylon variants improve load-bearing capacity, allowing usage in sturdy transmissions and farming equipment.
Quality assurance is prioritized via advanced CNC machining, injection molding, and 3D printing methods to achieve tolerances as limited as ± 0.005 mm. Rigorous testing, consisting of lots endurance, thermal cycling, and sound level checks, ensures integrity. Personalization choices include tooth account optimization, surface area layers for reduced rubbing, and UV stablizing for outdoor usage.
These plastic equipments are significantly replacing steel in applications where weight reduction, deterioration resistance, and price effectiveness are vital. Their smooth transmission abilities lessen energy loss, while high precision makes sure smooth combination right into intricate assemblies. Industries such as vehicle, aerospace, healthcare, and automation rely upon these gears for regular performance in demanding conditions, backed by ISO-certified production and customized design support.
Campony Introduction
Established in 2002, Shift Gear Machinery Co.,ltd. focus on metal research and mining machinery spare parts. 2 factories over an area of 13,300 square meters, based on 100+ sets of equipment, our production capacity reaches 12000 Tons/Year. has passed ISO 9001 quality managment system certification in 2008.
Our mainly products are dragline excavator spare parts,rotary kiln spare parts, large modulus gear (gear shaft), gearbox ect. 40+ patents with over 45 years experience to help focus on improve the service life of spare parts. We belive that more than 80% reason of mechanical parts’ working life depends on hot processing (steel making/forging/casting/welding/heat treatment). Eight material engineers will control the quality from the original resource.
If you are interested, please feel free to contact us.
Payment
L/C, T/T, Western Union, Paypal, Credit Card etc.
Shipment
By sea, by air, by express, as customers request.
5 FAQs of Factory Custom Quality Assurance Smooth Transmission Plastic Gear PP PEEK POM Nylon Gear With High Precision
What materials are used in your custom plastic gears, and why do they matter? Our factory uses PP, PEEK, POM, and nylon to manufacture plastic gears. PP (polypropylene) offers excellent chemical resistance and cost-effectiveness for light-duty applications. PEEK (polyetheretherketone) is ideal for high-temperature, high-stress environments due to its thermal stability and mechanical strength. POM (polyoxymethylene) ensures low friction and high dimensional stability, perfect for precision motion systems. Nylon provides superior wear resistance and toughness, making it suitable for dynamic loads. Material selection depends on your application’s operational demands, ensuring durability and performance.
How do you ensure high precision in plastic gears? We achieve high precision through advanced CNC machining and injection molding processes, paired with strict quality control. Tolerances as tight as ±0.005mm to ±0.01mm are maintained using precision tooling and automated inspection systems. Our engineers optimize gear geometry, tooth profiles, and surface finishes to minimize backlash and ensure smooth transmission. Post-production, gears undergo rigorous testing for dimensional accuracy, concentricity, and torque performance to meet exact specifications.
What quality assurance measures are in place? Our QA process includes ISO 9001-certified protocols, starting with raw material inspections to verify grade and purity. In-process checks monitor mold alignment, temperature, and pressure during production. Finished gears are tested for load capacity, wear resistance, noise levels, and thermal stability. We also provide material certification and performance test reports, ensuring compliance with international standards like ASTM or DIN.
Can you customize gear specifications for unique applications? Yes, we specialize in custom solutions. We adjust gear module sizes, pressure angles, helix angles, and bore diameters to match your requirements. Whether you need micro-gears for medical devices or large-diameter gears for industrial machinery, we tailor designs using CAD/CAM software and rapid prototyping. Custom material blends or additives (e.g., lubricants, glass fibers) can also be incorporated to enhance performance.
What industries typically use your plastic gears? Our gears serve automotive systems (seat adjusters, wiper mechanisms), aerospace components, medical devices (infusion pumps, surgical tools), robotics, and industrial automation. POM and nylon gears are popular in food processing and packaging machinery due to their FDA-compliance and low maintenance. PEEK gears excel in aerospace and oil/gas applications where heat and corrosion resistance are critical. Each gear is engineered to meet industry-specific regulatory and performance standards.
(Factory Custom Quality Assurance Smooth Transmission Plastic Gear PP PEEK POM Nylon Gear With High Precision)
REQUEST A QUOTE
RELATED PRODUCTS
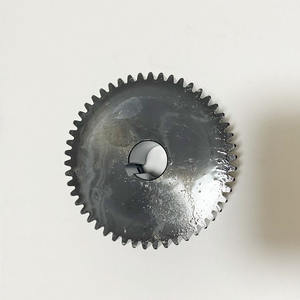
Customized Support OEM Planetary Reduction Gearbox for Drilling Rig and Truck Crane
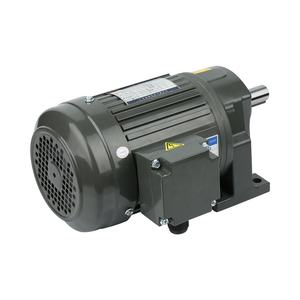
High Precision Gearbox Component Accessory Worm Gear and Worm Shaft for WPA NMRV Worm Gearbox
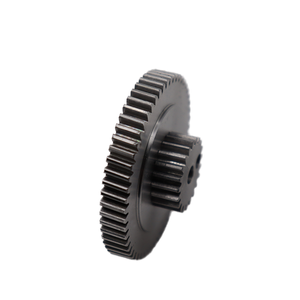
Linyao factory large forged high quality steel custom made internal gear for mechanical equipment
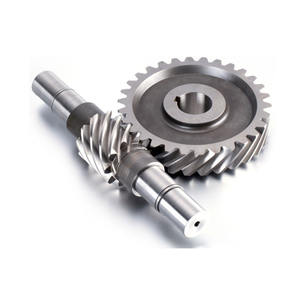
Hot oem high precision pu nylon spiral bevel gears plastic Worm & Helical Gear Set

Shenzhen HXMT FactoryGear Coupling Nylon Smooth Flat Nylon Gear Bearing Wheel Nylon Double Spur Gears
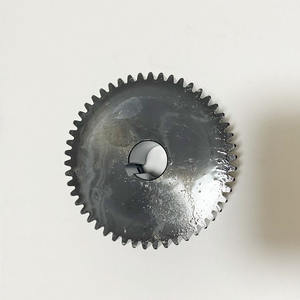