PRODUCT PARAMETERS
Description
Overview of Factory low custom large forged high-quality steel inner gear ring for mechanical equipment
Gears are mechanical elements that are typically used to transmit rotational motion and force. They work by meshing teeth with each other to change speed, direction of torque, or to transfer power between multiple shafts. Gears are an integral part of mechanical engineering and are widely used in a variety of mechanical devices.
Advantages and features of Factory low custom large forged high-quality steel inner gear ring for mechanical equipment
Efficient transmission: Gears are capable of directly converting power with high efficiency and low energy loss.
Precise ratios: the desired ratio of speed and torque can be obtained by selecting gears of different sizes.
Compact: Factory low custom large forged high-quality steel inner gear ring for mechanical equipmentsystems take up less space than other forms of power transmission.
High durability: well-designed gears can operate stably for long periods of time in harsh environments.
Low noise and vibration: Modern Factory low custom large forged high-quality steel inner gear ring for mechanical equipmentmanufacturing technology ensures smooth operation and reduces noise and vibration.
Various types: Spur, helical, and bevel gears are available depending on the application scenario.
(Factory low custom large forged high-quality steel inner gear ring for mechanical equipment)
Specifications of Factory low custom large forged high-quality steel inner gear ring for mechanical equipment
This factory-made custom-made huge built steel inner gear ring is made for sturdy mechanical tools. It deals with high-stress operations in industries such as mining, building, and manufacturing. The equipment ring is developed utilizing premium-grade steel alloy for stamina and durability. Products include carbon steel, alloy steel, or stainless steel, depending upon particular demands. The creating process makes sure a thick, consistent grain framework, improving load ability and resistance to put on.
The internal gear ring undergoes precise machining to satisfy precise dimensional demands. Teeth accounts are reduced with precision to make certain smooth involvement with mating equipments. Resistances are maintained tight, normally within ISO 1328-1 requirements. Surface surfaces are maximized to reduce friction and stop premature wear. Heat treatment procedures like quenching and tempering boost firmness while preserving durability.
Modification alternatives cover diameters from 500 mm to 5000 mm. Wall thickness and face size are flexible based on torque and rate demands. Tooth components range in between 10 mm and 50 mm. Flange designs, bolt opening patterns, and keyway setups can be tailored to fit existing equipment. Anti-corrosion finishes or plating solutions are readily available for rough atmospheres.
Quality checks consist of ultrasonic testing to find interior defects. Magnetic bit inspection verifies surface honesty. Dimensional accuracy is validated using coordinate gauging machines. Each equipment ring is marked with a distinct ID for traceability. Qualifications like ISO 9001 and ASTM A788 guarantee compliance with global standards.
The equipment ring operates in applications like rotary kilns, sphere mills, and crushers. It sustains high radial and axial lots without contortion. Routine upkeep entails lubrication checks and tooth surface area examinations. Extra components compatibility is assured with exact documentation.
Packaging makes use of rust-proof products and wood dog crates for safe shipping. Preparations differ based upon dimension and personalization. Technical support is attended to setup and troubleshooting. Bulk order discounts are available for lasting partnerships.
(Factory low custom large forged high-quality steel inner gear ring for mechanical equipment)
Applications of Factory low custom large forged high-quality steel inner gear ring for mechanical equipment
Factory low personalized large built top notch steel internal gear rings serve vital roles in sturdy mechanical systems. These components transfer power, manage high torque, and keep accurate movement control in commercial tools. Constructed for durability, they endure extreme functional stress and anxiety without failing.
Mining tools depends on these equipment rings. Excavators, crushers, and conveyor systems utilize them to take care of hefty lots during product removal. The created steel framework resists wear from rough settings. Construction equipment like cranes and bulldozers depend upon these components for smooth power transmission. They guarantee reputable efficiency under constant resonance and shock.
Heavy manufacturing equipment uses internal equipment rings in hydraulic presses and rolling mills. The parts take care of intense stress during metal forming. Accuracy tooth profiles minimize friction, expanding equipment life expectancy. Renewable energy systems like wind turbines incorporate these equipments to transform blades activity right into electricity. Their high toughness sustains continuous operation in extreme weather condition.
Customization permits customized options. Sizes range from one meter to over five meters in diameter. Tooth accounts match particular equipment harmonizing demands. Material grades adjust based on functional needs– high-carbon steel for firmness, alloy blends for rust resistance. Creating makes sure premium grain positioning compared to spreading. This improves exhaustion resistance and lots ability.
Manufacturing entails heating steel billets to high temperatures. Hydraulic presses shape the steel right into harsh equipment forms. CNC equipments complete the teeth to precise specs. Heat therapy enhances firmness and toughness. Surface therapies like shot peening reduce stress factors.
Quality checks include ultrasonic screening for inner imperfections. Dimensional examinations verify resistances within 0.05 mm. Lots testing mimics real-world conditions to verify performance. These actions make certain each equipment ring fulfills sector standards for safety and reliability.
The design focuses on very easy integration with existing systems. Installing surface areas and screw patterns straighten with common machinery designs. This lowers setup time and downtime throughout replacements. Regular maintenance entails lubrication and use tracking. Proper treatment expands life span even in 24/7 operations.
Campony Introduction
Established in 2002, Shift Gear Machinery Co.,ltd. focus on metal research and mining machinery spare parts. 2 factories over an area of 13,300 square meters, based on 100+ sets of equipment, our production capacity reaches 12000 Tons/Year. has passed ISO 9001 quality managment system certification in 2008.
Our mainly products are dragline excavator spare parts,rotary kiln spare parts, large modulus gear (gear shaft), gearbox ect. 40+ patents with over 45 years experience to help focus on improve the service life of spare parts. We belive that more than 80% reason of mechanical parts’ working life depends on hot processing (steel making/forging/casting/welding/heat treatment). Eight material engineers will control the quality from the original resource.
If you are interested, please feel free to contact us.
Payment
L/C, T/T, Western Union, Paypal, Credit Card etc.
Shipment
By sea, by air, by express, as customers request.
5 FAQs of Factory low custom large forged high-quality steel inner gear ring for mechanical equipment
What materials are used in the factory low custom large forged steel inner gear rings?
The inner gear rings are made from high-quality alloy steel. This steel is chosen for its strength and resistance to wear. The forging process compresses the steel to improve density and structural integrity. The result is a durable component capable of handling heavy loads and high stress in mechanical systems.
Can the inner gear rings be customized to fit specific equipment?
Yes. These gear rings are custom-made to match exact requirements. Dimensions, tooth profiles, and bore sizes are adjusted based on technical drawings or samples. Customization ensures compatibility with different types of machinery. Precision machining guarantees smooth integration into existing systems.
How does the forging process improve gear ring performance?
Forging aligns the steel’s grain structure, boosting toughness and fatigue resistance. It eliminates internal defects common in cast or machined parts. The process also enhances load distribution across the gear teeth. This reduces the risk of cracks or failures under operational stress.
What quality checks are performed during production?
Each gear ring undergoes rigorous testing. Ultrasonic inspections detect hidden flaws in the material. Hardness tests verify consistent surface strength. Dimensional checks ensure accuracy using laser measuring tools. Heat treatment is monitored to confirm optimal hardness and ductility. These steps guarantee compliance with industry standards.
What industries use these forged steel inner gear rings?
They are common in mining, construction, energy, and heavy manufacturing. Applications include gearboxes, rotary kilns, crushers, and large conveyors. The rings handle high-torque operations in harsh environments. Their reliability makes them suitable for critical machinery requiring long-term performance.
(Factory low custom large forged high-quality steel inner gear ring for mechanical equipment)
REQUEST A QUOTE
RELATED PRODUCTS
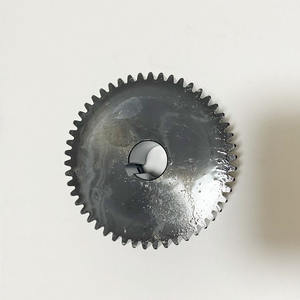
Power take off pto reversing gearbox gear boxes for agricultural machinery parts
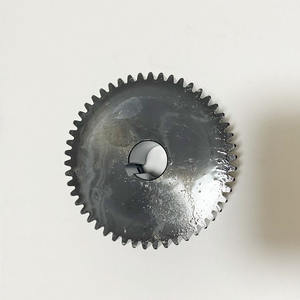
Custom Seat Motor Steel Gear Shaft Kit Suitable for 2007-2017 GMC Trucks
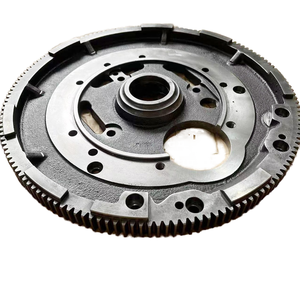
High End Customized Gear Housing Services CNC Laser Cutting Service Fabrication Sheet Metal Working

Aokman Solid Shaft Output Cyclo Gear Motor Cycloidal Gearbox for Power Industrial Transmission
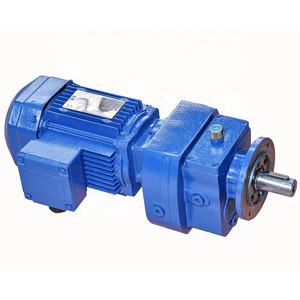
Cnc Machining Oem Factory Plastic Injection Products Plastic Nylon Gear Rack Non-Standard Accessories
