PRODUCT PARAMETERS
Description
Overview of High Precision Customized Construction Machinery Metal Gear
Gears are mechanical elements that are typically used to transmit rotational motion and force. They work by meshing teeth with each other to change speed, direction of torque, or to transfer power between multiple shafts. Gears are an integral part of mechanical engineering and are widely used in a variety of mechanical devices.
Advantages and features of High Precision Customized Construction Machinery Metal Gear
Efficient transmission: Gears are capable of directly converting power with high efficiency and low energy loss.
Precise ratios: the desired ratio of speed and torque can be obtained by selecting gears of different sizes.
Compact: High Precision Customized Construction Machinery Metal Gearsystems take up less space than other forms of power transmission.
High durability: well-designed gears can operate stably for long periods of time in harsh environments.
Low noise and vibration: Modern High Precision Customized Construction Machinery Metal Gearmanufacturing technology ensures smooth operation and reduces noise and vibration.
Various types: Spur, helical, and bevel gears are available depending on the application scenario.
(High Precision Customized Construction Machinery Metal Gear)
Specifications of High Precision Customized Construction Machinery Metal Gear
High Accuracy Customized Construction Machinery Steel Gears are crafted to fulfill the extensive demands of heavy-duty construction tools, ensuring resilience, effectiveness, and reliability in extreme operating environments. These equipments are made utilizing innovative CNC machining, hobbing, and grinding technologies to accomplish micron-level precision, crucial for seamless power transmission and minimized wear. The gears are crafted from state-of-the-art alloy steels, such as 4140, 4340, or stainless-steel, heat-treated via carburizing, induction solidifying, or nitriding to achieve surface firmness of 58-62 HRC and core sturdiness of 30-40 HRC, ensuring resistance to abrasion, influence, and fatigue. Customization choices include tailored measurements (outer size: 50mm to 2000mm; module: 2 to 20; teeth matter: 10 to 200), stress angles (14.5 °, 20 °, or 25 °), and tooth accounts (spur, helical, bevel, or global) to match particular equipment requirements. Precision resistances comply with AGMA 14-15 or ISO 1328 criteria, with reaction regulated within 0.05-0.15 mm for marginal noise and vibration. Surface area finish is brightened to Ra 0.8-1.6 μm to boost lubrication retention and minimize rubbing. Gears go through rigorous top quality checks, including CMM dimensions, ultrasonic screening, and lots simulation, ensuring conformity with ISO 9001 and CE qualifications. Personalized finishings (zinc-nickel, DLC, or powder coverings) are available for rust resistance in damp or chemically hostile environments. Applications include excavators, excavators, cranes, and concrete mixers, where high torque (up to 10,000 Nm) and rotational rates (200-3000 RPM) are critical. Preparations vary from 4-12 weeks based upon intricacy, with MOQs beginning at 50 units. Custom-made engineering assistance is attended to reverse design, prototyping, and combination with existing systems. Product packaging includes anti-rust VCI movies and wooden crates for safe international delivery. These gears are designed to prolong equipment life-span by 30-40% while minimizing downtime, making them perfect for OEMs and aftermarket distributors focusing on efficiency and cost-efficiency in construction tasks.
(High Precision Customized Construction Machinery Metal Gear)
Applications of High Precision Customized Construction Machinery Metal Gear
High accuracy customized building machinery metal equipments are crafted to satisfy the demanding requirements of modern-day construction projects, where reliability, longevity, and effectiveness are non-negotiable. These gears are indispensable to a variety of sturdy devices, making certain seamless power transmission, precise activity control, and prolonged operational life expectancies even under severe conditions. Their applications extend across excavators, excavators, cranes, loaders, and concrete mixers, where they play a crucial duty in enhancing performance and decreasing downtime.
In excavators and excavators, high accuracy metal equipments are essential for drivetrain systems, slewing systems, and hydraulic pumps. Personalized tooth profiles and heat-treated alloy steels make sure ideal tons distribution, reducing wear and tear while managing high torque and shock loads. For cranes and raising devices, these gears enable smooth lifting and turning, where micron-level precision prevents backlash and makes sure safe, controlled activities during heavy tons procedures. In concrete mixers and pavers, corrosion-resistant finishings and hardened surface areas fight unpleasant products, preserving equipment honesty in extreme, dusty environments.
Modification allows these gears to adjust to specific equipment layouts, spatial restrictions, and functional demands. Whether enhancing equipment proportions for gas effectiveness, modifying measurements to fit portable tools, or customizing products for extreme temperatures, bespoke services optimize compatibility and efficiency. Advanced manufacturing techniques like CNC machining and grinding make certain limited resistances, while limited aspect evaluation (FEA) validates equipment designs for stress and anxiety resistance and long life.
Past traditional construction lorries, these gears are vital in specialized equipment such as passage boring devices (TBMs) and loading rigs, where accuracy alignment and durability are crucial for underground or deep-foundation job. They likewise support automatic and telematics-enabled tools, contributing to smarter, data-driven building and construction processes.
By minimizing friction, noise, and power loss, high accuracy equipments improve functional effectiveness and sustainability, decreasing upkeep prices and carbon footprints. Their duty in decreasing devices failure makes certain job timelines remain on track, making them a cornerstone of modern-day construction development. For sectors focusing on performance and customization, these equipments stand for a blend of engineering excellence and sensible adaptability, driving efficiency in every turning.
Campony Introduction
Established in 2002, Shift Gear Machinery Co.,ltd. focus on metal research and mining machinery spare parts. 2 factories over an area of 13,300 square meters, based on 100+ sets of equipment, our production capacity reaches 12000 Tons/Year. has passed ISO 9001 quality managment system certification in 2008.
Our mainly products are dragline excavator spare parts,rotary kiln spare parts, large modulus gear (gear shaft), gearbox ect. 40+ patents with over 45 years experience to help focus on improve the service life of spare parts. We belive that more than 80% reason of mechanical parts’ working life depends on hot processing (steel making/forging/casting/welding/heat treatment). Eight material engineers will control the quality from the original resource.
If you are interested, please feel free to contact us.
Payment
L/C, T/T, Western Union, Paypal, Credit Card etc.
Shipment
By sea, by air, by express, as customers request.
5 FAQs of High Precision Customized Construction Machinery Metal Gear
1. **What customization options are available for high-precision construction machinery metal gears?** Customization options include material selection (such as alloy steel, stainless steel, or carbon steel), gear dimensions (diameter, module, tooth count), tooth profile modifications (spur, helical, or custom designs), surface treatments (heat treatment, nitriding, or coatings), and load capacity adjustments. Tailored solutions are designed to meet specific operational requirements, environmental conditions, and compatibility with existing machinery.
2. **How is high precision achieved in custom metal gears?** Precision is ensured through advanced CNC machining, gear hobbing, grinding, and finishing processes. Computer-aided design (CAD) and simulation tools optimize gear geometry for smooth meshing and minimal backlash. Quality control involves coordinate measuring machines (CMM) and laser inspection to verify micron-level tolerances, ensuring gears meet exact specifications for performance and durability.
3. **What materials are best suited for heavy-duty construction machinery gears?** Alloy steels like 4140 or 4340 are preferred for their high strength, wear resistance, and ability to withstand extreme loads. Case-hardened or carburized surfaces enhance durability. For corrosive environments, stainless steel or coated alloys are recommended. Material choice is finalized based on application-specific stress, temperature, and environmental factors.
4. **How long does it take to manufacture custom metal gears?** Lead times vary depending on design complexity, material availability, and order volume. Standard projects take 4–8 weeks, including prototyping, testing, and production. Rush services may be available for critical projects, but maintaining precision and quality remains a priority.
5. **Do your gears comply with industry standards?** Yes, our gears adhere to international standards like ISO 1328, AGMA 2015, and DIN 3961 for accuracy, noise control, and load capacity. Certifications such as ISO 9001 ensure consistent quality. We also perform real-world testing (fatigue, torque, stress) to validate performance under construction machinery conditions.
(High Precision Customized Construction Machinery Metal Gear)
REQUEST A QUOTE
RELATED PRODUCTS
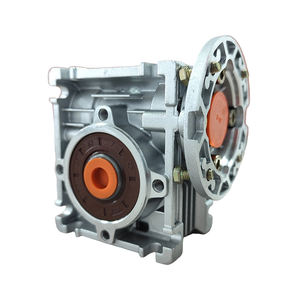
Large Diameter Metal Spur Gear for Transmission Machines
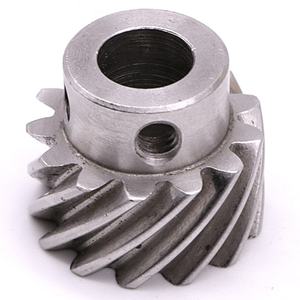
High Quality Not Easy To Break Good Transmission Rate Engine Fixed Gear For The Automotive Industry
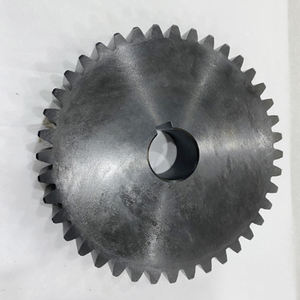
Custom Small Metal Spur Gear Steel And Special Gears Manufacture
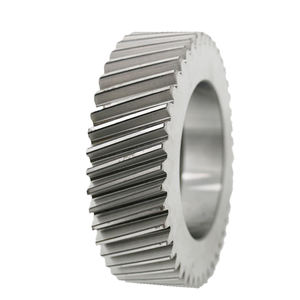