PRODUCT PARAMETERS
Description
Overview of High precision gear powder metallurgy sintered parts are customized by the powder metallurgy gear
Gears are mechanical elements that are typically used to transmit rotational motion and force. They work by meshing teeth with each other to change speed, direction of torque, or to transfer power between multiple shafts. Gears are an integral part of mechanical engineering and are widely used in a variety of mechanical devices.
Advantages and features of High precision gear powder metallurgy sintered parts are customized by the powder metallurgy gear
Efficient transmission: Gears are capable of directly converting power with high efficiency and low energy loss.
Precise ratios: the desired ratio of speed and torque can be obtained by selecting gears of different sizes.
Compact: High precision gear powder metallurgy sintered parts are customized by the powder metallurgy gearsystems take up less space than other forms of power transmission.
High durability: well-designed gears can operate stably for long periods of time in harsh environments.
Low noise and vibration: Modern High precision gear powder metallurgy sintered parts are customized by the powder metallurgy gearmanufacturing technology ensures smooth operation and reduces noise and vibration.
Various types: Spur, helical, and bevel gears are available depending on the application scenario.
(High precision gear powder metallurgy sintered parts are customized by the powder metallurgy gear)
Specifications of High precision gear powder metallurgy sintered parts are customized by the powder metallurgy gear
High precision gear powder metallurgy sintered parts are made using advanced powder metallurgy methods. These parts are designed for custom applications requiring exact shapes, strong performance, and long-lasting use. The process starts with metal powders like iron, steel, or stainless steel. These powders are mixed, pressed into molds, and heated to form solid metal parts. This method allows tight control over dimensions, ensuring gears meet strict tolerance requirements.
The main advantage of powder metallurgy gears is their high accuracy. Complex shapes and detailed tooth profiles are achievable without extra machining. This reduces production time and costs. The process also minimizes material waste compared to traditional methods like cutting or casting. Parts made this way have uniform density and structure, improving strength and wear resistance.
Customization is a key feature. Gear dimensions, tooth counts, and load capacities are adjusted to fit specific needs. Industries like automotive, aerospace, and machinery benefit from parts tailored to unique operating conditions. Heat treatments or coatings are added to boost hardness or reduce friction. This flexibility makes the gears suitable for high-stress environments.
Material options vary based on application demands. Iron-based powders are common for cost-effective solutions. Steel alloys provide higher strength, while stainless steel offers corrosion resistance. Lubricants or additives are mixed into the powder to enhance performance. This ensures smooth operation and reduces maintenance needs.
Quality control is critical. Each batch undergoes checks for size, density, and surface finish. Testing methods include dimensional inspection, hardness measurement, and load testing. This guarantees parts meet industry standards like ISO or ASTM certifications. Consistent quality ensures reliability in critical applications.
These sintered gears are used in motors, transmissions, pumps, and industrial equipment. Their precision reduces noise and vibration, improving overall system efficiency. The process supports both small and large production runs, making it adaptable to different project scales. By combining customization, material efficiency, and high performance, powder metallurgy gears provide a practical solution for modern engineering challenges.
(High precision gear powder metallurgy sintered parts are customized by the powder metallurgy gear)
Applications of High precision gear powder metallurgy sintered parts are customized by the powder metallurgy gear
High precision gear powder metallurgy sintered parts are manufactured using specialized powder metallurgy methods. These parts serve critical roles across multiple industries. The automotive sector uses them in transmissions, engine systems, and electric vehicle components. They handle heavy loads and last long. Their exact shapes improve efficiency and reduce operational noise.
Aerospace applications include landing gear systems and flight control mechanisms. These gears are light but strong. This reduces fuel use and maintains safety. Custom designs meet strict industry requirements.
Medical equipment relies on these parts for surgical tools and diagnostic machines. Tiny, precise gears are essential here. Powder metallurgy creates complex shapes without extra machining. This cuts production costs. Materials chosen are safe for medical use.
Industrial machinery uses these gears in robotics and heavy-duty equipment. Custom sizes and shapes fit specific functions. They resist wear and high temperatures. This lowers maintenance needs and downtime.
Consumer electronics like printers and home appliances use these sintered parts. They ensure smooth operation and compact designs. Manufacturers save costs while maintaining reliability.
Powder metallurgy allows full customization of gears. Engineers collaborate with clients to meet exact needs. Material properties like strength or corrosion resistance can be adjusted. Production is efficient with minimal material waste.
This approach is cost-effective for large-scale production. It skips expensive machining steps. Tight tolerances guarantee uniform quality. Industries receive high-performance parts designed for their unique demands.
Campony Introduction
Established in 2002, Shift Gear Machinery Co.,ltd. focus on metal research and mining machinery spare parts. 2 factories over an area of 13,300 square meters, based on 100+ sets of equipment, our production capacity reaches 12000 Tons/Year. has passed ISO 9001 quality managment system certification in 2008.
Our mainly products are dragline excavator spare parts,rotary kiln spare parts, large modulus gear (gear shaft), gearbox ect. 40+ patents with over 45 years experience to help focus on improve the service life of spare parts. We belive that more than 80% reason of mechanical parts’ working life depends on hot processing (steel making/forging/casting/welding/heat treatment). Eight material engineers will control the quality from the original resource.
If you are interested, please feel free to contact us.
Payment
L/C, T/T, Western Union, Paypal, Credit Card etc.
Shipment
By sea, by air, by express, as customers request.
5 FAQs of High precision gear powder metallurgy sintered parts are customized by the powder metallurgy gear
High precision gear powder metallurgy sintered parts are custom-made using metal powders. The process involves pressing powdered materials into shapes under high pressure. The shaped parts are heated in a controlled environment to bond particles. This creates strong, durable gears with tight tolerances. Common materials include iron, steel, and alloy blends. The method suits complex geometries hard to achieve with traditional machining.
These parts save costs. Powder metallurgy reduces material waste. It eliminates multiple machining steps. The process allows high-volume production with consistent quality. Gears made this way handle high loads and resist wear. They work well in automotive and industrial machinery. The final parts often need no extra finishing. This cuts production time and expense.
Customization starts with design specifications. Engineers use CAD models to define gear dimensions and tooth profiles. Material selection depends on application needs. Production tools are designed for pressing and sintering. Prototypes are tested for performance under real conditions. Adjustments are made before full-scale manufacturing. Tolerances as tight as ±0.03mm are achievable. This ensures parts fit perfectly in assemblies.
These gears are used in cars, robots, power tools, and medical devices. Examples include transmission gears, engine components, and precision actuators. The parts handle high torque and operate quietly. Their porous structure can be impregnated with lubricants. This extends service life in demanding environments. Industries choose them for reliability and cost savings over machined or cast alternatives.
Powder metallurgy competes with machining and casting. It beats machining in cost for complex shapes and high volumes. It outperforms casting in dimensional accuracy. Machined gears may have better surface finish for some uses. Cast gears can be cheaper for very large sizes. Powder metallurgy balances precision, strength, and affordability. It is ideal for mid-to-high volume orders needing exact specifications.
(High precision gear powder metallurgy sintered parts are customized by the powder metallurgy gear)
REQUEST A QUOTE
RELATED PRODUCTS

China Hot Powder Metallurgy Motor Gear Stainless Steel Gear Parts Powder Metallurgy Gear
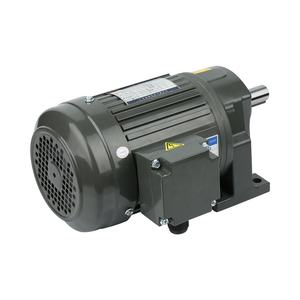
Power take off pto reversing gearbox gear boxes for agricultural machinery parts
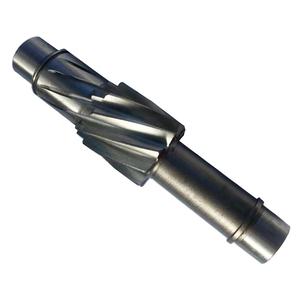
Custom made small modulus spur Gears large module brass copper steel aluminum nylon pom plastic pinion gears
Knotted gears – Used to supply custom parts at Massey Ferguson Original Equipment Large square baler plant
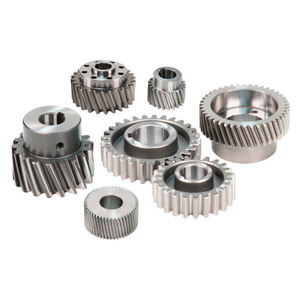
HXMT Customized Carbon Steel Alloy Steel Stainless Steel Shaft Gear Cnc Machining From Shenzhen Factory
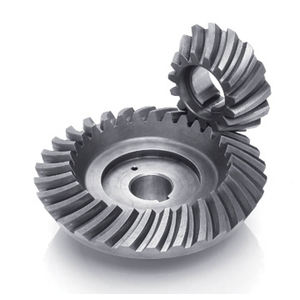