PRODUCT PARAMETERS
Description
Overview of High precision gear powder metallurgy sintered parts are customized by the powder metallurgy gear
Gears are mechanical elements that are typically used to transmit rotational motion and force. They work by meshing teeth with each other to change speed, direction of torque, or to transfer power between multiple shafts. Gears are an integral part of mechanical engineering and are widely used in a variety of mechanical devices.
Advantages and features of High precision gear powder metallurgy sintered parts are customized by the powder metallurgy gear
Efficient transmission: Gears are capable of directly converting power with high efficiency and low energy loss.
Precise ratios: the desired ratio of speed and torque can be obtained by selecting gears of different sizes.
Compact: High precision gear powder metallurgy sintered parts are customized by the powder metallurgy gearsystems take up less space than other forms of power transmission.
High durability: well-designed gears can operate stably for long periods of time in harsh environments.
Low noise and vibration: Modern High precision gear powder metallurgy sintered parts are customized by the powder metallurgy gearmanufacturing technology ensures smooth operation and reduces noise and vibration.
Various types: Spur, helical, and bevel gears are available depending on the application scenario.
(High precision gear powder metallurgy sintered parts are customized by the powder metallurgy gear)
Specifications of High precision gear powder metallurgy sintered parts are customized by the powder metallurgy gear
High accuracy equipment powder metallurgy sintered components are used innovative powder metallurgy methods. These components are designed for customized applications. The process begins with metal powders like iron, steel, or stainless-steel. The powders are pressed into a mold and mildew under high stress. This produces a compact shape near the last equipment style. The compressed part is warmed in a controlled heater. The temperature is below the melting factor. This bonds the steel particles securely. The outcome is a strong, thick component with very little material waste.
The equipments achieve limited resistances. Normal dimensional precision varieties from ± 0.05 mm to ± 0.1 mm. Surface area roughness is kept in between Ra 1.6 and Ra 3.2 micrometers. This makes certain smooth procedure and reduced noise. The components handle high tons and withstand wear. Heat treatment alternatives like carburizing or relieving boost firmness. Surface therapies like oil impregnation or finishings improve deterioration resistance.
Modification is an essential attribute. Gears can be made in different dimensions, shapes, and tooth profiles. Usual types consist of spur equipments, helical gears, and bevel gears. Adjustments to gear teeth, hubs, or keyways are possible. The process sustains complicated geometries. This stays clear of costly machining steps. Powder metallurgy allows mixing products for certain properties. Iron-copper blends improve toughness. Self-lubricating products minimize rubbing.
Quality assurance is rigorous. Each batch undergoes look for density, solidity, and measurements. Tons screening mimics real-world problems. X-ray or ultrasonic evaluations identify internal defects. This guarantees reliability sought after applications.
These equipments are utilized in automotive transmissions, commercial machinery, and power devices. They fit robotics, medical gadgets, and aerospace systems. Advantages include price financial savings, decreased waste, and quicker manufacturing. Powder metallurgy consumes to 97% of resources. Traditional techniques waste as much as 40%. No extra machining is needed for most parts. This cuts production time. The process is environment-friendly. It uses much less power and generates less exhausts compared to casting or creating.
(High precision gear powder metallurgy sintered parts are customized by the powder metallurgy gear)
Applications of High precision gear powder metallurgy sintered parts are customized by the powder metallurgy gear
High precision gear powder metallurgy sintered components are specialized elements made by compacting metal powders and warming them to form solid frameworks. These components serve critical roles across numerous sectors due to their precision, longevity, and ability to be personalized. Manufacturers depend on powder metallurgy gears due to the fact that the process permits limited control over dimensions and product homes. This makes the components perfect for applications where efficiency and integrity issue.
In the automobile market, these gears are used in transmissions, steering systems, and engine elements. Their high toughness and put on resistance aid vehicles manage heavy lots and duplicated stress. The aerospace market uses them in actuators, touchdown equipment systems, and flight control systems. The components have to stand up to severe temperatures and stress while preserving accuracy. Medical tools like surgical devices and imaging devices additionally utilize these equipments. Smooth procedure and rust resistance are vital below to ensure patient safety and tool longevity.
Industrial equipment relies on powder metallurgy equipments for robotics, conveyor systems, and heavy tools. The gears lower friction and noise, boosting efficiency in high-speed procedures. Customization is a vital benefit. Manufacturers readjust gear dimension, form, and product make-up to satisfy specific needs. Complicated geometries or special tooth accounts are attainable without pricey machining. This adaptability quicken production and cuts expenses.
Product waste is minimized in powder metallurgy contrasted to standard techniques. The process makes use of almost all resources, making it affordable and eco-friendly. Parts usually need little finishing job, conserving time and sources. High accuracy gears made by doing this constantly meet strict quality criteria. They perform reliably in rough conditions, from high temperatures to harsh environments. Industries worth these parts for their balance of efficiency, price, and flexibility.
Campony Introduction
Established in 2002, Shift Gear Machinery Co.,ltd. focus on metal research and mining machinery spare parts. 2 factories over an area of 13,300 square meters, based on 100+ sets of equipment, our production capacity reaches 12000 Tons/Year. has passed ISO 9001 quality managment system certification in 2008.
Our mainly products are dragline excavator spare parts,rotary kiln spare parts, large modulus gear (gear shaft), gearbox ect. 40+ patents with over 45 years experience to help focus on improve the service life of spare parts. We belive that more than 80% reason of mechanical parts’ working life depends on hot processing (steel making/forging/casting/welding/heat treatment). Eight material engineers will control the quality from the original resource.
If you are interested, please feel free to contact us.
Payment
L/C, T/T, Western Union, Paypal, Credit Card etc.
Shipment
By sea, by air, by express, as customers request.
5 FAQs of High precision gear powder metallurgy sintered parts are customized by the powder metallurgy gear
High precision gear powder metallurgy sintered parts are made by pressing metal powders into shapes. The parts are heated to bond particles. This creates strong gears with tight tolerances. These gears fit applications needing exact performance.
Customization works by adjusting the powder mix and mold design. Engineers create molds matching specific gear shapes and sizes. Adjustments happen during pressing and sintering. This ensures gears meet exact load, speed, or noise requirements.
Common materials include iron, steel, and stainless steel powders. Alloy blends add strength or corrosion resistance. Material choice depends on gear use. Coatings like zinc or nickel improve durability in harsh environments.
Benefits over traditional gears include lower costs and less material waste. Powder metallurgy forms complex shapes in one step. Machining gears from solid metal takes longer and costs more. Sintered gears have uniform structures. This makes them durable under stress.
These gears are used in cars, planes, and industrial machines. Car transmissions use them for smooth power transfer. Plane systems rely on their lightweight strength. Factories use them in robots and heavy equipment. Any device needing precise movement can use sintered gears.
(High precision gear powder metallurgy sintered parts are customized by the powder metallurgy gear)
REQUEST A QUOTE
RELATED PRODUCTS
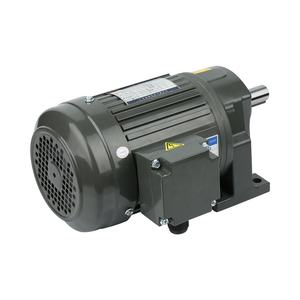
Steel Precision tooth gearbox 60 size 45Nm small backlash 5 arcmin for nema 24 and nema 23 servo stepper bldc motors bevel gear
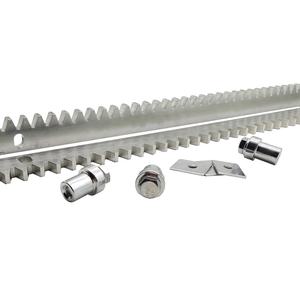
Whole Custom Gear Shape resin 7pcs pink Dices set For DND tabletop rpg game
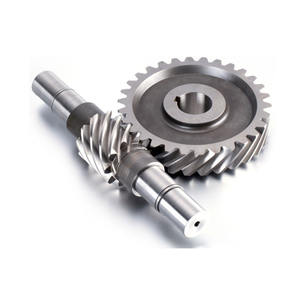
factory low casting durable transmission large diameter gear wheel for mining machinery
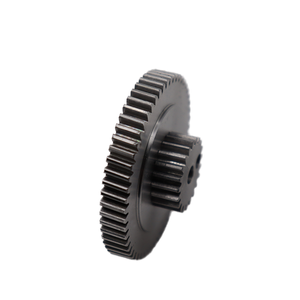
Linyao factory large forged high quality steel custom made internal gear for mechanical equipment

TILI TVB Close Loop Stepper Right Angle 90 Degree Flange Servo Motor Speed Reducer Nema23 Nema34 Nema42 Planetary Gearbox
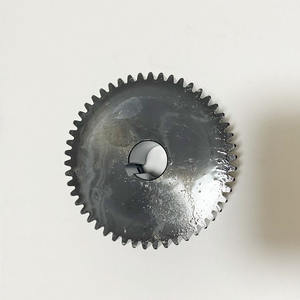