PRODUCT PARAMETERS
Description
Overview of High Precision Straight Bevel Gear CNC Machining Spur Bevel Gear
Gears are mechanical elements that are typically used to transmit rotational motion and force. They work by meshing teeth with each other to change speed, direction of torque, or to transfer power between multiple shafts. Gears are an integral part of mechanical engineering and are widely used in a variety of mechanical devices.
Advantages and features of High Precision Straight Bevel Gear CNC Machining Spur Bevel Gear
Efficient transmission: Gears are capable of directly converting power with high efficiency and low energy loss.
Precise ratios: the desired ratio of speed and torque can be obtained by selecting gears of different sizes.
Compact: High Precision Straight Bevel Gear CNC Machining Spur Bevel Gearsystems take up less space than other forms of power transmission.
High durability: well-designed gears can operate stably for long periods of time in harsh environments.
Low noise and vibration: Modern High Precision Straight Bevel Gear CNC Machining Spur Bevel Gearmanufacturing technology ensures smooth operation and reduces noise and vibration.
Various types: Spur, helical, and bevel gears are available depending on the application scenario.
(High Precision Straight Bevel Gear CNC Machining Spur Bevel Gear)
Specifications of High Precision Straight Bevel Gear CNC Machining Spur Bevel Gear
High Accuracy Straight Bevel Gear CNC Machining Spur Bevel Equipment is crafted for demanding applications needing demanding accuracy, longevity, and smooth power transmission in between intersecting shafts. These gears are made utilizing innovative CNC machining innovation, ensuring tight resistances, regular quality, and optimum efficiency in commercial, auto, aerospace, and robotics systems.
** Material Options: ** Available in high-strength alloy steel (e.g., 20CrMnTi, 4140), stainless-steel (304/316), and hard carbon steel (1045, 4340). Warm therapy procedures like carburizing, induction hardening, or nitriding improve surface hardness (as much as 58-62 HRC) and wear resistance. Personalized material demands are fit for specialized atmospheres.
** Trick Requirements: **.
– ** Gear Module/Pitch: ** Component range 1– 10 (metric) or diametral pitch 20– 5 (imperial).
– ** Pearly whites Matter: ** 10– 50 teeth, personalized to meet certain ratio needs.
– ** Stress Angle: ** Standard 20 °, with 25 ° choices for high-load applications.
– ** Pitch Diameter: ** 20mm– 500mm, scalable based on style demands.
– ** Shaft Angle: ** Usually 90 °, flexible for non-perpendicular setups.
** Accuracy Tolerances: **.
– ** Tooth Profile Precision: ** AGMA Q10 or ISO 1328 Class 5 standards.
– ** Surface Complete: ** 0.8– 1.6 µm Ra for minimized friction and sound.
– ** Backlash Control: ** Adjustable in between 0.05– 0.15 mm to balance accuracy and operational level of smoothness.
– ** Runout Tolerance: ** ≤ 0.02 mm for concentricity and very little vibration.
** CNC Machining Advantages: **.
– 5-axis CNC devices guarantee specific tooth geometry, consistent spacing, and flawless surface honesty.
– CAD/CAM-driven procedures enable fast prototyping and repeatability for bulk orders.
– Custom-made tooth accounts, birthed sizes, keyways, and placing configurations are supported.
** Applications: ** Suitable for differential systems, power tools, aquatic propulsion, wind generators, and precision equipment requiring high torque and angular activity transfer.
** Quality control: ** Each equipment goes through rigorous examination by means of CMM, gear testers, and firmness testers. Dimensional reports, material certifications, and load-testing data are provided.
** Packaging & Distribution: ** Anti-corrosion coated and vacuum-sealed for security. Standard lead time is 2– 4 weeks, with expedited choices for urgent needs.
This equipment remedy integrates innovative production, robust materials, and strict quality assurance to provide reliability in high-stress atmospheres while reducing operational noise and energy loss.
(High Precision Straight Bevel Gear CNC Machining Spur Bevel Gear)
Applications of High Precision Straight Bevel Gear CNC Machining Spur Bevel Gear
High precision straight bevel gears made via CNC machining are critical elements in industries needing demanding standards for power transmission and activity control. These gears, known for their conical form and straight teeth, make it possible for effective torque transfer in between intersecting shafts at 90-degree angles. CNC machining makes sure phenomenal precision, repeatability, and surface area finish, making them excellent for applications where reliability and efficiency are non-negotiable.
In the automobile field, high accuracy straight bevel equipments are used in differential systems to disperse power equally between wheels, enhancing grip and handling. Their CNC-machined tolerances lessen noise and vibration, improving car resilience and guest convenience. Likewise, aerospace applications depend on these gears for touchdown gear systems, helicopter transmissions, and flight control systems, where lightweight yet durable components are crucial for safety and security and efficiency under extreme conditions.
Industrial machinery gain from CNC-machined straight bevel equipments in heavy-duty equipment like printing presses, conveyor systems, and maker devices. Their exact tooth accounts make certain smooth involvement, decreasing wear and downtime in high-load atmospheres. Robotics and automation systems also take advantage of these gears for specific angular activity in robot arms and articulated joints, enabling high-speed, accurate procedures in production and assembly lines.
Renewable energy systems, such as wind generators, utilize straight bevel gears in yaw and pitch control devices to optimize blade alignment with wind instructions. CNC machining ensures the sturdiness required to endure severe ecological problems while keeping operational effectiveness. In medical gadgets, these equipments are indispensable to imaging tools and medical robots, where silent, backlash-free activity is important for accuracy and patient safety.
The marine sector uses CNC-machined straight bevel equipments in propulsion systems and guiding devices, using deterioration resistance and dependability in saltwater atmospheres. Customization by means of CNC allows customized options for distinct torque and speed demands across markets. By incorporating innovative products like solidified steel or aerospace-grade alloys with CNC accuracy, these gears deliver long life, lowered upkeep, and improved performance, strengthening their role as important parts in modern design remedies.
Campony Introduction
Established in 2002, Shift Gear Machinery Co.,ltd. focus on metal research and mining machinery spare parts. 2 factories over an area of 13,300 square meters, based on 100+ sets of equipment, our production capacity reaches 12000 Tons/Year. has passed ISO 9001 quality managment system certification in 2008.
Our mainly products are dragline excavator spare parts,rotary kiln spare parts, large modulus gear (gear shaft), gearbox ect. 40+ patents with over 45 years experience to help focus on improve the service life of spare parts. We belive that more than 80% reason of mechanical parts’ working life depends on hot processing (steel making/forging/casting/welding/heat treatment). Eight material engineers will control the quality from the original resource.
If you are interested, please feel free to contact us.
Payment
L/C, T/T, Western Union, Paypal, Credit Card etc.
Shipment
By sea, by air, by express, as customers request.
5 FAQs of High Precision Straight Bevel Gear CNC Machining Spur Bevel Gear
What is a high-precision straight bevel gear? A high-precision straight bevel gear is a mechanical component with straight teeth cut along conical surfaces, designed to transmit motion and power between intersecting shafts at a 90-degree angle. These gears are manufactured using CNC machining to ensure exact tooth profiles, minimal backlash, and smooth meshing, making them ideal for applications requiring high accuracy, such as aerospace, automotive systems, and industrial machinery.
How does CNC machining improve the quality of spur bevel gears? CNC machining uses computer-controlled tools to achieve micron-level precision in gear manufacturing. This process ensures consistent tooth geometry, tight tolerances (typically within ±0.005 mm), and superior surface finishes. Unlike traditional methods, CNC reduces human error, enables complex designs, and enhances repeatability, resulting in gears with optimized load distribution, reduced noise, and extended service life.
What materials are commonly used for high-precision straight bevel gears? Common materials include alloy steels (e.g., 4140, 4340), stainless steel (e.g., 304, 316), and thermoplastics like nylon or PEEK. Steel alloys are preferred for high-strength and durability in heavy-load applications, while stainless steel offers corrosion resistance. Plastics are used for lightweight, low-noise operations in industries like food processing or robotics.
Where are CNC-machined spur bevel gears typically applied? These gears are widely used in precision-driven industries, including automotive differentials, helicopter rotor systems, medical equipment, robotics, and power tools. They excel in scenarios requiring efficient torque transfer, directional changes, and compact designs, such as steering mechanisms, conveyor systems, and rotary actuators.
How do I maintain high-precision straight bevel gears for longevity? Regular lubrication with industry-approved greases or oils minimizes wear and friction. Inspect gears periodically for pitting, misalignment, or abnormal noise. Avoid overloading and ensure proper alignment during installation. Store gears in clean, dry environments to prevent corrosion. Partnering with a certified manufacturer for routine maintenance or replacements ensures optimal performance and durability.
(High Precision Straight Bevel Gear CNC Machining Spur Bevel Gear)
REQUEST A QUOTE
RELATED PRODUCTS
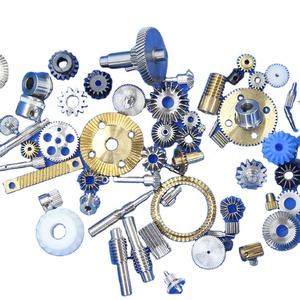
Precision Worm Gear And Shaft Made In China Gear Wheel Straight Tooth Gear Worm Wheel,Worm Gear,Gear Worm Gear
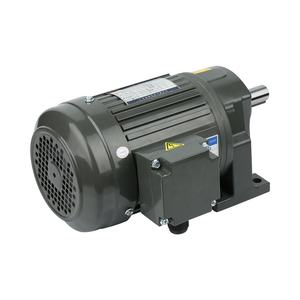
OEM Customized Stainless Steel Gear Parts CNC Machining With Turned Finish New Condition Custom Services
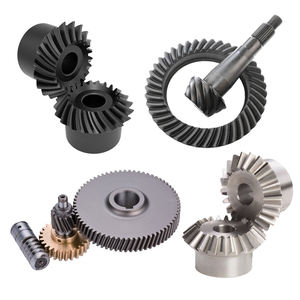
Cnc Precision Machining Service Titanium Cnc Machining Milling Turning Gear Parts
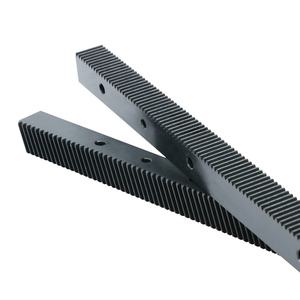
Custom Planetary Gear Cnc Machining Pinion Gears Steel Gears
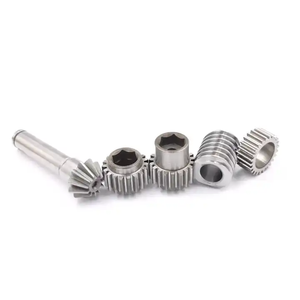