PRODUCT PARAMETERS
Description
Overview of High Quality Hot val machining high precision Nylon big gear
Gears are mechanical elements that are typically used to transmit rotational motion and force. They work by meshing teeth with each other to change speed, direction of torque, or to transfer power between multiple shafts. Gears are an integral part of mechanical engineering and are widely used in a variety of mechanical devices.
Advantages and features of High Quality Hot val machining high precision Nylon big gear
Efficient transmission: Gears are capable of directly converting power with high efficiency and low energy loss.
Precise ratios: the desired ratio of speed and torque can be obtained by selecting gears of different sizes.
Compact: High Quality Hot val machining high precision Nylon big gearsystems take up less space than other forms of power transmission.
High durability: well-designed gears can operate stably for long periods of time in harsh environments.
Low noise and vibration: Modern High Quality Hot val machining high precision Nylon big gearmanufacturing technology ensures smooth operation and reduces noise and vibration.
Various types: Spur, helical, and bevel gears are available depending on the application scenario.
(High Quality Hot val machining high precision Nylon big gear)
Specifications of High Quality Hot val machining high precision Nylon big gear
High-quality hot-axis machining on large, precision nylon gears can be achieved with several key specifications. First and foremost, the gear should have a minimum surface finish that is consistent across all teeth to ensure proper engagement and wear resistance.
In addition to the surface finish, the gear must also meet the specific requirements for its application. For example, if the gear will be used in a severe environment where heat exposure is significant, it may need to be designed with higher strength and durability materials.
One important aspect of high-quality hot-axis machining is the selection of appropriate tools and equipment. The tools used to cut and shape the gears must be capable of producing accurate and precise cutting results, while also being able to handle the large and heavy load required by the machine.
Another critical factor in achieving high-quality hot-axis machining on large, precision nylon gears is the use of specialized techniques such as automatic boring machines and advanced grinding machines. These techniques can help to eliminate operator error and improve overall efficiency, while also reducing the amount of material waste produced during the manufacturing process.
Overall, high-quality hot-axis machining on large, precision nylon gears requires careful consideration of a range of technical specifications, including surface finish, tool selection, and machine operation. By following these guidelines, manufacturers can produce high-quality that meet or exceed even the most demanding performance requirements.
(High Quality Hot val machining high precision Nylon big gear)
Applications of High Quality Hot val machining high precision Nylon big gear
High-quality hot vulcanizing is an important process in the production of nylon gears. This type of operation involves heating the nylon material to a high temperature and then applying heat to cause it to flow into small holes or grooves in a steel die.
One of the key benefits of using high-quality hot vulcanizing is that it results in gears with greater accuracy and precision than those made with traditional methods. This is because the heat applied during the vulcanization process causes the nylon material to flow more smoothly and evenly, resulting in smaller imperfections in the gears. Additionally, the use of high-quality materials can improve the lifespan of the gears, as they are less likely to become damaged or worn out due to the heat and pressure used during the vulcanization process.
Another benefit of using high-quality hot vulcanizing is that it can result in faster tool changes, as the gears can be quickly removed and replaced without damaging them. This can be particularly useful in applications where time is of the essence, such as in the automotive industry, where fast turnaround times are crucial for meeting customer demands.
In addition to these benefits, high-quality hot vulcanizing can also provide additional advantages over other manufacturing processes. For example, it can reduce waste by minimizing the need for replacement parts, and it can help to reduce emissions by reducing the amount of energy needed to heat and cool the nylon material.
Overall, the use of high-quality hot vulcanizing can result in gears with increased accuracy, precision, and durability, as well as faster tool changes and reduced waste. As such, it is an important process in the production of nylon gears, and is often preferred over other methods of manufacturing due to its many benefits.
Campony Introduction
Established in 2002, Shift Gear Machinery Co.,ltd. focus on metal research and mining machinery spare parts. 2 factories over an area of 13,300 square meters, based on 100+ sets of equipment, our production capacity reaches 12000 Tons/Year. has passed ISO 9001 quality managment system certification in 2008.
Our mainly products are dragline excavator spare parts,rotary kiln spare parts, large modulus gear (gear shaft), gearbox ect. 40+ patents with over 45 years experience to help focus on improve the service life of spare parts. We belive that more than 80% reason of mechanical parts’ working life depends on hot processing (steel making/forging/casting/welding/heat treatment). Eight material engineers will control the quality from the original resource.
If you are interested, please feel free to contact us.
Payment
L/C, T/T, Western Union, Paypal, Credit Card etc.
Shipment
By sea, by air, by express, as customers request.
5 FAQs of High Quality Hot val machining high precision Nylon big gear
1. What is high quality hot vacuum machining and why is it important forNylon?
High-quality hot vacuum machining (HTVM) is a process that uses high vacuum and extremely high temperatures to remove material from a workpiece without causing damage or warping.
ForNylon, HTVM is essential because the final product must be highly precise and have minimal wear and tear. By using HTVM, manufacturers can produce gears with even wear patterns and smooth surfaces, which reduces maintenance costs and increases overall efficiency.
2. How does HTVM compare to other methods for manufacturing precision Nylons?
HTVM is generally considered to be one of the most accurate methods for manufacturing precision Nylons. It allows manufacturers to produce gears with a uniform finish and excellent accuracy, which is difficult or impossible to achieve with traditional methods such as heat treatment or machining.
In addition, HTVM uses fewer chemicals and produces less waste than traditional methods, making it an environmentally friendly option.
3. What kind of equipment is needed for HTVM and how does it work?
To perform high-quality hot vacuum machining on Nylons, manufacturers typically use specialized equipment such as vacuum machines, chiller systems, and milling machines. The equipment works by creating a very high vacuum environment around the workpiece, which draws out impurities and wear particles while allowing the metal to remain at high temperatures.
The melted polymer is then drained away and recoated, resulting in a highly finished product with low levels of wear and tear.
4. Can HTVM be used on all types of Nylons?
Not all Nylons are suitable for HTVM. Some materials may not be compatible with the vacuum and temperature conditions required for the process, or they may require special coatings or treatments to improve their compatibility with HTVM equipment.
However, most Nylons are suitable for HTVM and can provide good results with careful consideration of the specific properties of the material being processed.
5. Are there any potential drawbacks or limitations to HTVM for manufacturing precision Nylons?
Yes, there are some potential drawbacks and limitations to HTVM for manufacturing precision Nylons. One limitation is that HTVM requires high temperatures and pressures, which can cause problems with the integrity of the material if not properly controlled.
Another potential issue is that HTVM can cause surface defects or weakened parts of the gear if not performed correctly. To mitigate these risks, manufacturers should follow established guidelines for HTVM usage and carefully monitor the results of each job to ensure consistent and reliable performance.
(High Quality Hot val machining high precision Nylon big gear)
REQUEST A QUOTE
RELATED PRODUCTS

CNC Aluminum Gearbox Skid Plate Transmission Mount for 1/18 Redcat Ascent-18 RC Upgrade Part
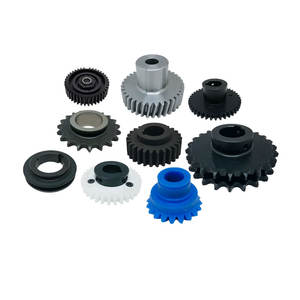
R series R17 R37 R57 High Quality Gearbox and Motor 50Hz Speed Reducer Coaxial Solid Shaft Electric Industrial Helical Gearmotor
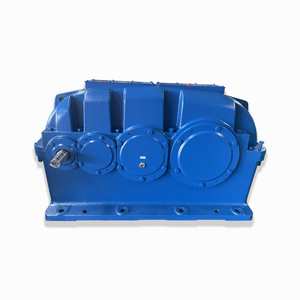
Factory Custom Molded High Precision Plastic Gears With Metal Hubs For High-Torque Applications
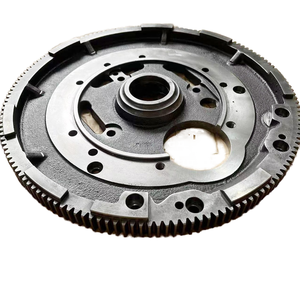
Gear Manufacturing Custom Cnc Machining Services For Precision Spur And Steel Gears Tailored For Oem Fabrications
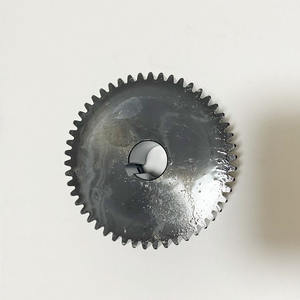
low custom casting durable transmission large gear ring for mining machinery
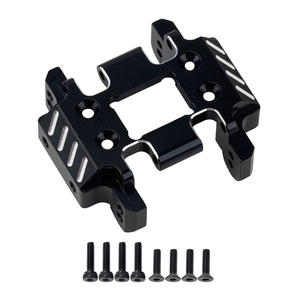