PRODUCT PARAMETERS
Description
Overview of Knotted gears – Used to supply custom parts at Massey Ferguson Original Equipment Large square baler plant
Gears are mechanical elements that are typically used to transmit rotational motion and force. They work by meshing teeth with each other to change speed, direction of torque, or to transfer power between multiple shafts. Gears are an integral part of mechanical engineering and are widely used in a variety of mechanical devices.
Advantages and features of Knotted gears – Used to supply custom parts at Massey Ferguson Original Equipment Large square baler plant
Efficient transmission: Gears are capable of directly converting power with high efficiency and low energy loss.
Precise ratios: the desired ratio of speed and torque can be obtained by selecting gears of different sizes.
Compact: Knotted gears – Used to supply custom parts at Massey Ferguson Original Equipment Large square baler plantsystems take up less space than other forms of power transmission.
High durability: well-designed gears can operate stably for long periods of time in harsh environments.
Low noise and vibration: Modern Knotted gears – Used to supply custom parts at Massey Ferguson Original Equipment Large square baler plantmanufacturing technology ensures smooth operation and reduces noise and vibration.
Various types: Spur, helical, and bevel gears are available depending on the application scenario.
(Knotted gears – Used to supply custom parts at Massey Ferguson Original Equipment Large square baler plant)
Specifications of Knotted gears – Used to supply custom parts at Massey Ferguson Original Equipment Large square baler plant
Knotted gears designed for Massey Ferguson Original Equipment (OEM) large square balers are precision-engineered components critical to the reliable operation of agricultural machinery. These gears are manufactured to meet exacting standards, ensuring compatibility with Massey Ferguson’s demanding performance requirements. Constructed from high-grade alloy steel or case-hardened carbon steel, they undergo heat treatment processes such as carburizing or induction hardening to achieve superior surface hardness (typically 55-62 HRC) and core toughness, enhancing wear resistance and longevity under heavy-load conditions. The gears feature precise tooth profiles, optimized for smooth meshing and minimal noise during high-speed operations, with tolerances adhering to AGMA (American Gear Manufacturers Association) standards. Key specifications include module ranges of 4-10, pressure angles of 20° or 25°, and custom pitch diameters tailored to baler models like the MF 2200 or MF RB Series. Bore diameters are machined to match OEM shaft specifications, often including keyways or splines for secure torque transmission. Surface finishes are polished to reduce friction, and anti-corrosion coatings (e.g., zinc-nickel or phosphate) are applied to withstand harsh field environments. Load capacities exceed 500 Nm, with fatigue resistance tested over 10^7 cycles to ensure reliability in continuous baling operations. Customization options include modifications for torque requirements, RPM ranges (up to 1500 RPM), and integration with baler knotter systems for synchronized twine tying. Quality assurance involves 100% dimensional inspection via CMM (Coordinate Measuring Machine) and load-testing protocols to validate performance under simulated operational stress. These gears are designed to replace or upgrade existing components in Massey Ferguson balers, ensuring minimal downtime and compliance with OEM service life expectations (10,000+ hours). Lead times for custom orders typically range from 4-6 weeks, with documentation including material certifications, hardness reports, and installation guidelines. Technical support is available for fitment validation and troubleshooting, backed by warranties covering material and workmanship defects.
(Knotted gears – Used to supply custom parts at Massey Ferguson Original Equipment Large square baler plant)
Applications of Knotted gears – Used to supply custom parts at Massey Ferguson Original Equipment Large square baler plant
Knotted gears are specialized mechanical components designed for heavy-duty applications, playing a critical role in the reliable operation of agricultural machinery such as Massey Ferguson’s Original Equipment Large Square Balers. These gears are engineered to deliver precision, durability, and high torque transmission, making them ideal for the demanding environments of hay and straw baling. At Massey Ferguson’s manufacturing plants, custom knotted gears are integrated into balers to ensure seamless performance, enabling farmers to produce tightly compacted, uniform bales efficiently.
The primary application of knotted gears in large square balers lies in their ability to handle extreme mechanical stress during the baling process. These gears are integral to the baler’s knotting system, which binds bales with twine or netting. Their unique knotted design enhances load distribution, reducing wear and tear even under continuous high-pressure cycles. Customized to Massey Ferguson’s specifications, these gears are manufactured with high-grade materials such as hardened steel or alloy composites, ensuring resistance to corrosion, abrasion, and fatigue. This customization allows precise alignment with the baler’s drivetrain, optimizing power transfer and minimizing energy loss.
Massey Ferguson relies on knotted gears to maintain the reliability of their balers, which are essential during time-sensitive harvest seasons. The gears’ robust construction reduces downtime caused by component failure, supporting uninterrupted operation in fields. Additionally, their precision engineering contributes to consistent bale density and shape, critical for storage, transport, and livestock feed quality.
Collaboration between Massey Ferguson and gear manufacturers ensures that each knotted gear meets stringent performance and safety standards. Advanced CNC machining and quality control processes guarantee dimensional accuracy, while tailored heat treatment enhances surface hardness and core toughness. This partnership underscores a commitment to innovation, enabling the development of gears that withstand variable field conditions, from heavy moisture to abrasive dust.
By incorporating custom knotted gears, Massey Ferguson’s Large Square Baler Plant delivers equipment that combines longevity with operational efficiency. Farmers benefit from reduced maintenance costs, extended service intervals, and enhanced productivity, reinforcing Massey Ferguson’s reputation as a leader in agricultural machinery. Knotted gears exemplify the fusion of traditional mechanical principles with modern engineering advancements, driving sustainability and performance in global farming operations.
Campony Introduction
Established in 2002, Shift Gear Machinery Co.,ltd. focus on metal research and mining machinery spare parts. 2 factories over an area of 13,300 square meters, based on 100+ sets of equipment, our production capacity reaches 12000 Tons/Year. has passed ISO 9001 quality managment system certification in 2008.
Our mainly products are dragline excavator spare parts,rotary kiln spare parts, large modulus gear (gear shaft), gearbox ect. 40+ patents with over 45 years experience to help focus on improve the service life of spare parts. We belive that more than 80% reason of mechanical parts’ working life depends on hot processing (steel making/forging/casting/welding/heat treatment). Eight material engineers will control the quality from the original resource.
If you are interested, please feel free to contact us.
Payment
L/C, T/T, Western Union, Paypal, Credit Card etc.
Shipment
By sea, by air, by express, as customers request.
5 FAQs of Knotted gears – Used to supply custom parts at Massey Ferguson Original Equipment Large square baler plant
What are knotted gears, and what role do they play in a Massey Ferguson large square baler? Knotted gears are critical components in the knotting system of a square baler, responsible for creating and securing knots on twine or netting during the baling process. These gears ensure consistent, reliable tying to maintain bale integrity, preventing unraveling during handling or transport. Custom-designed for Massey Ferguson equipment, they operate under high stress, requiring precision engineering to synchronize with the baler’s timing and motion.
How do I know if a knotted gear is compatible with my Massey Ferguson baler model? Knotted gears are tailored to specific Massey Ferguson baler models and production years. Compatibility depends on factors like gear dimensions, tooth profile, and mounting specifications. Always reference your baler’s serial number or consult the OEM parts manual to confirm the correct gear variant. Custom replacements are machined to match original design schematics, ensuring seamless integration with existing systems.
What materials are used in manufacturing custom knotted gears, and how durable are they? Knotted gears are typically forged from high-grade alloy steel or case-hardened metals to withstand heavy loads, abrasion, and repetitive motion. Advanced heat treatment or coatings like nitriding may be applied to enhance wear resistance. These materials ensure longevity even in demanding conditions, though lifespan depends on operational intensity, maintenance practices, and environmental factors like debris exposure.
Are custom knotted gears readily available, or do they require long lead times? As specialized components, knotted gears are often made-to-order to meet exact OEM specifications. Lead times vary based on production schedules and customization complexity, but suppliers prioritize Massey Ferguson OEM partners to minimize downtime. Stock availability for common models may exist, but urgent orders can sometimes be expedited—confirm with the supplier for real-time updates.
What maintenance practices extend the life of knotted gears in a square baler? Regular inspection and lubrication are key. Check gears for tooth wear, cracks, or misalignment during routine service. Use lubricants recommended by Massey Ferguson to reduce friction and heat buildup. Clean gears to prevent debris accumulation, which accelerates wear. Replace gears immediately if they show pitting, chipping, or fail to maintain knotting consistency, as delayed repairs can damage adjacent components.
(Knotted gears – Used to supply custom parts at Massey Ferguson Original Equipment Large square baler plant)
REQUEST A QUOTE
RELATED PRODUCTS
Factory customized large forged high-quality steel inner gear for mechanical equipment
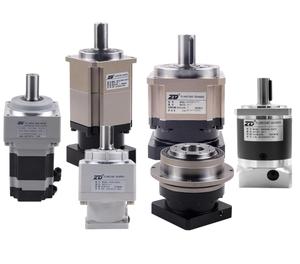
Nylon gear POM plastic straight gear peek oblique abrasion -resistant high -temperature precision non -standard processing
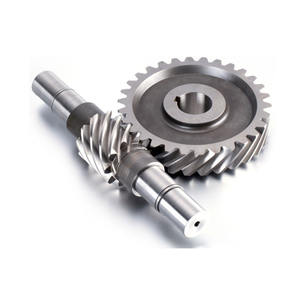
P2L Bevel gear Stage Industrial Gearbox Industrial Planetary Reducer For New Energy Industry

Hot 4140 Alloy Steel Forged Gear Ring For Construction Machinery, Forging Slewing Bearing With CNC Machining For Marine
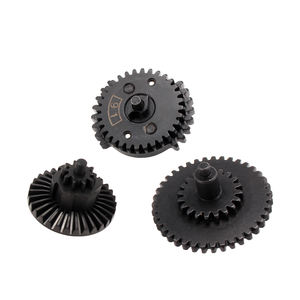
8223072 Gear Selector Transmission Controller Transmission Shifter For Engine Diesel Excavator Spare Parts
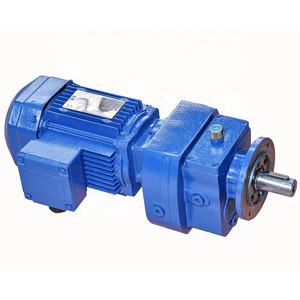