PRODUCT PARAMETERS
Description
Overview of OEM Ball Mill Casting Large Diameter Spur Gear Rotary Dryer Blender cement rotary kiln girth gear
Gears are mechanical elements that are typically used to transmit rotational motion and force. They work by meshing teeth with each other to change speed, direction of torque, or to transfer power between multiple shafts. Gears are an integral part of mechanical engineering and are widely used in a variety of mechanical devices.
Advantages and features of OEM Ball Mill Casting Large Diameter Spur Gear Rotary Dryer Blender cement rotary kiln girth gear
Efficient transmission: Gears are capable of directly converting power with high efficiency and low energy loss.
Precise ratios: the desired ratio of speed and torque can be obtained by selecting gears of different sizes.
Compact: OEM Ball Mill Casting Large Diameter Spur Gear Rotary Dryer Blender cement rotary kiln girth gearsystems take up less space than other forms of power transmission.
High durability: well-designed gears can operate stably for long periods of time in harsh environments.
Low noise and vibration: Modern OEM Ball Mill Casting Large Diameter Spur Gear Rotary Dryer Blender cement rotary kiln girth gearmanufacturing technology ensures smooth operation and reduces noise and vibration.
Various types: Spur, helical, and bevel gears are available depending on the application scenario.
(OEM Ball Mill Casting Large Diameter Spur Gear Rotary Dryer Blender cement rotary kiln girth gear)
Specifications of OEM Ball Mill Casting Large Diameter Spur Gear Rotary Dryer Blender cement rotary kiln girth gear
The OEM Ball Mill Casting Big Diameter Spur Equipment is crafted for heavy-duty industrial applications, featuring high-strength alloy steel (e.g., ASTM A148/SAE 4340) with specific heat treatment for improved wear resistance. Regular diameters range from 1m to 10m, with face widths approximately 1.5 m, components of 10– 40, and solidity degrees of 280– 320 HB. Customized tooth profiles make sure smooth meshing and decreased vibration, supporting torque abilities up to 5,000 kNm. Rotary Dryer Blender or food processor Gears are made for blending and drying out systems, utilizing long lasting carbon or low-alloy steel with induction-hardened teeth (HRC 50– 55) for abrasion resistance. Usual components range from 12– 30, with diameters approximately 8m and face sizes of 600– 1,200 mm. Precision-ground teeth reduce sound and enhance power transmission. The Concrete Rotary Kiln Girth Gear is constructed to endure severe thermal and mechanical stress, crafted from high-grade cast steel (ZG270-500/ ZG310-570) with stabilized and toughened up treatment for consistent firmness (200– 240 HB). Diameters extend 3m– 12m, face widths 400– 1,000 mm, and modules 20– 50. These gears incorporate split styles for simple setup and maintain positioning under heavy radial lots (as much as 10,000 kN). All gears undergo rigorous quality checks, including ultrasonic testing and dimensional confirmation, ensuring conformity with ISO 9001 standards. Customization alternatives include screw patterns, lubrication systems, and flange arrangements to match specific equipment. Applications cover concrete plants, mining, metallurgy, and chemical industries, providing prolonged service life with very little maintenance. OEM support includes reverse design, on-site measurement, and performance optimization for smooth assimilation with sphere mills, rotating kilns, and clothes dryers.
(OEM Ball Mill Casting Large Diameter Spur Gear Rotary Dryer Blender cement rotary kiln girth gear)
Applications of OEM Ball Mill Casting Large Diameter Spur Gear Rotary Dryer Blender cement rotary kiln girth gear
OEM ball mill casting large size spur equipments are essential parts in heavy-duty grinding equipment used throughout mining, concrete production, and mineral processing sectors. These gears transfer power effectively in between the electric motor and the turning drum, making it possible for the sphere mill to squash and grind resources right into fine powders. Their large diameter and accuracy spreading ensure durability under high-torque problems, reducing wear and maintenance downtime. Custom-engineered to match details operational needs, these spur equipments are heat-treated for boosted hardness and fatigue resistance, making them perfect for continual, high-load applications. Rotary dryer blender or food processors rely upon durable spur gears to help with the mixing and drying out of mass products such as fertilizers, chemicals, and foodstuff. The gears make sure synchronized rotation of the drum, advertising uniform heat distribution and product consistency. Their corrosion-resistant design matches damp or high-temperature environments, expanding life span. In concrete manufacturing, rotary kiln girth equipments are important for driving the slow-moving turning of the kiln, which heats raw materials to generate clinker. These large gears withstand extreme thermal tension, hefty lots, and rough conditions. Precision-machined teeth accounts make sure smooth interaction with pinions, minimizing vibration and power loss. OEM girth gears are typically custom-fabricated with high-grade alloy steel and advanced surface area therapies to combat wear, making certain placement with kiln specifications for ideal performance. With each other, these components exhibit crafted remedies for industrial machinery, providing dependability, performance, and durability. OEM making warranties customized measurements, material high quality, and compliance with market requirements, sustaining seamless integration right into existing systems. By lowering operational disturbances and maintenance expenses, these gears improve productivity in sectors where constant processing is critical. Their applications highlight the importance of precision engineering in heavy equipment, where component failure can cause significant manufacturing losses. Purchasing top notch OEM equipments guarantees operational durability and sustains the requiring cycles of industries like concrete, mining, and bulk product processing.
Campony Introduction
Established in 2002, Shift Gear Machinery Co.,ltd. focus on metal research and mining machinery spare parts. 2 factories over an area of 13,300 square meters, based on 100+ sets of equipment, our production capacity reaches 12000 Tons/Year. has passed ISO 9001 quality managment system certification in 2008.
Our mainly products are dragline excavator spare parts,rotary kiln spare parts, large modulus gear (gear shaft), gearbox ect. 40+ patents with over 45 years experience to help focus on improve the service life of spare parts. We belive that more than 80% reason of mechanical parts’ working life depends on hot processing (steel making/forging/casting/welding/heat treatment). Eight material engineers will control the quality from the original resource.
If you are interested, please feel free to contact us.
Payment
L/C, T/T, Western Union, Paypal, Credit Card etc.
Shipment
By sea, by air, by express, as customers request.
5 FAQs of OEM Ball Mill Casting Large Diameter Spur Gear Rotary Dryer Blender cement rotary kiln girth gear
What materials are used in OEM ball mill, rotary dryer, and cement kiln girth gears?
These gears are manufactured using high-strength alloy steels such as 42CrMo, 35CrMo, or custom grades tailored to operational demands. The materials undergo heat treatment processes like quenching, tempering, or carburizing to enhance hardness, wear resistance, and load-bearing capacity, ensuring durability in high-stress, high-temperature environments.
How are large diameter spur gears precision-engineered for heavy machinery?
OEM large diameter spur gears are produced via advanced casting techniques followed by CNC machining and gear hobbing to achieve precise tooth profiles and dimensional accuracy. Strict quality checks, including ultrasonic testing and hardness verification, ensure optimal meshing, minimal vibration, and seamless integration with ball mills, rotary dryers, blenders, or kilns.
Can these gears be customized for specific equipment requirements?
Yes. OEM services allow full customization in diameter (up to 10 meters or more), module, tooth count, bore size, and flange design to match original equipment specs. Custom heat treatment, surface coatings, or alloy compositions can also be applied to suit unique operational conditions like abrasive materials or extreme temperatures.
What maintenance practices prolong the lifespan of cement kiln girth gears and rotary dryer gears?
Regular lubrication with high-viscosity gear oils prevents friction and overheating. Alignment checks between gear and pinion ensure even load distribution. Periodic inspections for cracks, pitting, or tooth wear, coupled with prompt replacement of damaged sections, minimize downtime. Protective covers or seals can reduce debris ingress in harsh environments.
Which industries rely on these large gears, and what are their key applications?
These gears are critical in cement plants (rotary kilns, ball mills), mining (ore grinding mills), chemical processing (rotary dryers, mixers), and metallurgy. They transmit high torque to rotate kilns, dryers, or mills, handling loads up to hundreds of tons. Their robust design supports continuous 24/7 operations, making them essential for bulk material processing and industrial manufacturing.
(OEM Ball Mill Casting Large Diameter Spur Gear Rotary Dryer Blender cement rotary kiln girth gear)
REQUEST A QUOTE
RELATED PRODUCTS
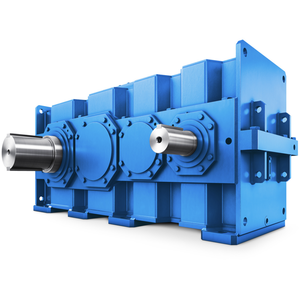
Custom Brass Gear Watch Dial Cnc Machining Kitchen Part

Aluminum Alloy Stainless Steel Wheel Accessories Primary Gear Wheel Bearing Gear

Flat Reduction 2Nm – 12Nm 12volt Gearbox Motor Dc gear Motor Gearbox 24v 12v Dc High Torque Electric Motor
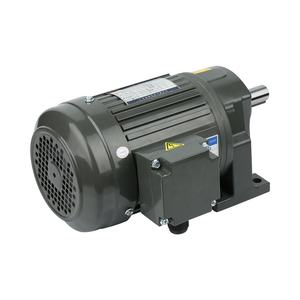
Power take off pto reversing gearbox gear boxes for agricultural machinery parts
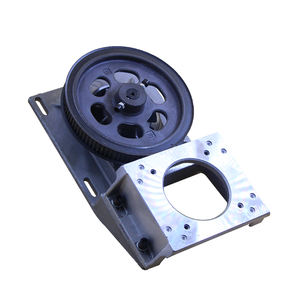
High Precision Customized Spur Gear Small Gears Pinion
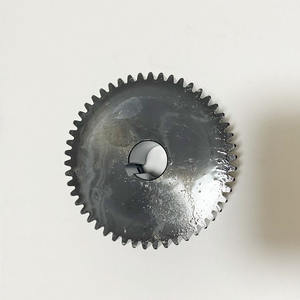