PRODUCT PARAMETERS
Description
Overview of OEM Machining Small Nylon Spur gear Plastic Helical gear Matching gear
Gears are mechanical elements that are typically used to transmit rotational motion and force. They work by meshing teeth with each other to change speed, direction of torque, or to transfer power between multiple shafts. Gears are an integral part of mechanical engineering and are widely used in a variety of mechanical devices.
Advantages and features of OEM Machining Small Nylon Spur gear Plastic Helical gear Matching gear
Efficient transmission: Gears are capable of directly converting power with high efficiency and low energy loss.
Precise ratios: the desired ratio of speed and torque can be obtained by selecting gears of different sizes.
Compact: OEM Machining Small Nylon Spur gear Plastic Helical gear Matching gearsystems take up less space than other forms of power transmission.
High durability: well-designed gears can operate stably for long periods of time in harsh environments.
Low noise and vibration: Modern OEM Machining Small Nylon Spur gear Plastic Helical gear Matching gearmanufacturing technology ensures smooth operation and reduces noise and vibration.
Various types: Spur, helical, and bevel gears are available depending on the application scenario.
(OEM Machining Small Nylon Spur gear Plastic Helical gear Matching gear)
Specifications of OEM Machining Small Nylon Spur gear Plastic Helical gear Matching gear
The OEM Machining Small Nylon Spur Gear and Plastic Helical Gear are precision-engineered components designed for a wide range of industrial and mechanical applications. These gears are crafted from high-quality nylon, offering exceptional durability, wear resistance, and low friction, making them ideal for smooth and efficient power transmission. The spur gear features straight teeth that are parallel to the gear axis, ensuring reliable performance in applications requiring high-speed rotation and minimal noise. On the other hand, the helical gear boasts angled teeth that provide smoother and quieter operation, making it suitable for high-load and high-speed applications where reduced vibration is critical.
Both gears are available in a variety of sizes, with customizable specifications to meet specific OEM requirements. The small nylon spur gear typically comes in diameters ranging from 5mm to 50mm, with module sizes from 0.5 to 2.5, while the helical gear offers similar dimensions with helix angles ranging from 15° to 45° for optimal performance. The gears are manufactured using advanced CNC machining techniques, ensuring precise tooth profiles, tight tolerances, and consistent quality. They are lightweight yet robust, capable of withstanding moderate to high loads without compromising performance.
The matching gear set is designed to work seamlessly together, ensuring smooth meshing and efficient power transfer. The nylon material provides excellent resistance to corrosion, chemicals, and moisture, making these gears suitable for use in harsh environments. Additionally, the self-lubricating properties of nylon reduce the need for frequent maintenance, enhancing operational efficiency and longevity.
These gears are widely used in industries such as automotive, robotics, medical devices, consumer electronics, and industrial machinery. Whether you need a reliable spur gear for straightforward applications or a helical gear for more complex, high-performance systems, this OEM machining solution delivers unmatched precision, durability, and versatility. Customization options include material grades, tooth profiles, and surface finishes to meet specific application needs.
(OEM Machining Small Nylon Spur gear Plastic Helical gear Matching gear)
Applications of OEM Machining Small Nylon Spur gear Plastic Helical gear Matching gear
OEM machining of small nylon spur gears and plastic helical gears, along with their matching counterparts, plays a pivotal role in a wide range of industries due to their precision, durability, and versatility. These gears are engineered to meet the specific requirements of original equipment manufacturers (OEMs), ensuring seamless integration into various applications. Nylon, as a material, offers exceptional properties such as lightweight construction, high wear resistance, low friction, and noise reduction, making it ideal for gear manufacturing.
Small nylon spur gears are commonly used in applications requiring straightforward power transmission with minimal noise. They are widely employed in consumer electronics, such as printers, cameras, and small household appliances, where compact size and quiet operation are essential. Additionally, they are utilized in automotive components, medical devices, and robotics, where precision and reliability are critical.
Plastic helical gears, on the other hand, are designed for applications that demand smoother and quieter operation at higher speeds. Their angled teeth allow for gradual engagement, reducing vibration and noise while improving load distribution. These gears are often found in industrial machinery, conveyor systems, and automotive transmissions, where efficiency and durability are paramount.
Matching gears, whether spur or helical, are custom-designed to work in tandem with their counterparts, ensuring optimal performance and longevity. OEM machining ensures that these gears are manufactured to exact specifications, with tight tolerances and consistent quality. This precision is crucial for applications in aerospace, defense, and high-performance machinery, where even the slightest deviation can lead to system failure.
The adaptability of nylon and plastic gears to various environments, including those with exposure to moisture, chemicals, or temperature fluctuations, further enhances their appeal. OEM machining allows for customization in terms of size, tooth profile, and material composition, ensuring that the gears meet the unique demands of each application. With their combination of lightweight design, durability, and precision, small nylon spur gears, plastic helical gears, and their matching counterparts continue to drive innovation across industries.
Campony Introduction
Established in 2002, Shift Gear Machinery Co.,ltd. focus on metal research and mining machinery spare parts. 2 factories over an area of 13,300 square meters, based on 100+ sets of equipment, our production capacity reaches 12000 Tons/Year. has passed ISO 9001 quality managment system certification in 2008.
Our mainly products are dragline excavator spare parts,rotary kiln spare parts, large modulus gear (gear shaft), gearbox ect. 40+ patents with over 45 years experience to help focus on improve the service life of spare parts. We belive that more than 80% reason of mechanical parts’ working life depends on hot processing (steel making/forging/casting/welding/heat treatment). Eight material engineers will control the quality from the original resource.
If you are interested, please feel free to contact us.
Payment
L/C, T/T, Western Union, Paypal, Credit Card etc.
Shipment
By sea, by air, by express, as customers request.
5 FAQs of OEM Machining Small Nylon Spur gear Plastic Helical gear Matching gear
(OEM Machining Small Nylon Spur gear Plastic Helical gear Matching gear)
REQUEST A QUOTE
RELATED PRODUCTS
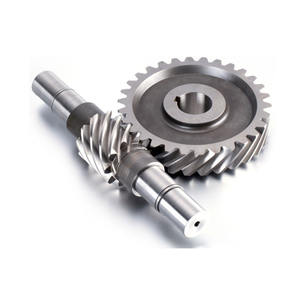
High Accuracy OEM Machining Cnc Milling Transmission Part Oxide Black Stainless Steel Wheel Spur gear
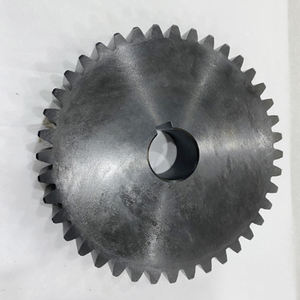
Custom Small Metal Spur Gear Steel And Special Gears Manufacture
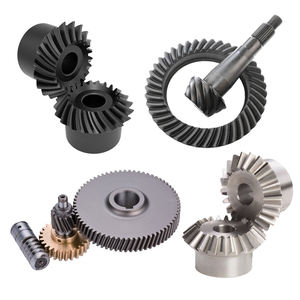
Highly Precision Spur gear Pinion gear
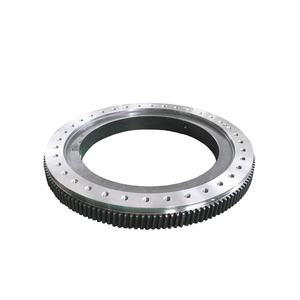
Aloma Factory Custom High Quality Fiberglass Diving Fins Freestyle Training Long Fins Snorkeling Gear
Custom According To Drawing Steel Rail Rack Spur Helical Cnc Gear Rack
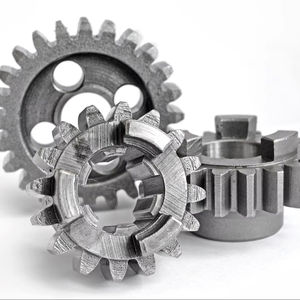