PRODUCT PARAMETERS
Description
Overview of Plastic gears Design And Processing
Gears are mechanical elements that are typically used to transmit rotational motion and force. They work by meshing teeth with each other to change speed, direction of torque, or to transfer power between multiple shafts. Gears are an integral part of mechanical engineering and are widely used in a variety of mechanical devices.
Advantages and features of Plastic gears Design And Processing
Efficient transmission: Gears are capable of directly converting power with high efficiency and low energy loss.
Precise ratios: the desired ratio of speed and torque can be obtained by selecting gears of different sizes.
Compact: Plastic gears Design And Processingsystems take up less space than other forms of power transmission.
High durability: well-designed gears can operate stably for long periods of time in harsh environments.
Low noise and vibration: Modern Plastic gears Design And Processingmanufacturing technology ensures smooth operation and reduces noise and vibration.
Various types: Spur, helical, and bevel gears are available depending on the application scenario.
(Plastic gears Design And Processing)
Specifications of Plastic gears Design And Processing
Plastic gears are vital elements in numerous sectors, using lightweight, corrosion-resistant, and economical alternatives to steel gears. Their layout and handling require cautious consideration of product residential or commercial properties, geometry, and production strategies to guarantee optimum performance. Below are the crucial requirements and factors to consider for plastic gear style and handling:
** Material Selection: ** Common products include polyoxymethylene (POM/acetal), nylon (), polycarbonate (PC), and polyethylene (PE). Each product supplies distinct residential properties– POM gives reduced friction and high tightness, nylon excels in sturdiness and use resistance, PC is suitable for high-impact applications, and PE is used for chemical resistance. Additives like glass fibers or lubricating substances are often integrated to improve strength, minimize friction, or improve thermal stability.
** Design Requirements: ** Equipment geometry have to follow standards such as AGMA (American Equipment Manufacturers Organization) or ISO (International Organization for Standardization). Vital specifications include module (pitch), stress angle (usually 20 °), tooth account (involute or cycloidal), and backlash tolerance. Wall thickness and center style are optimized to avoid deformation under tons. Finite component evaluation (FEA) is used to replicate stress and anxiety circulation and forecast failure points.
** Processing Approaches: ** Shot molding is the key production approach, allowing high-volume production with tight tolerances ( ± 0.02– 0.05 mm). Mold and mildew layout requires specific cooling channels to decrease bending. For low-volume or custom-made gears, CNC machining or 3D printing (using materials like abdominal or polyamide) may be utilized. Post-processing actions include annealing to alleviate interior tensions, surface area completing (polishing), and lubrication (silicone or PTFE coverings) to decrease noise and wear.
** Efficiency Considerations: ** Plastic equipments are sensitive to temperature level changes, moisture absorption, and continual tons. Running temperatures typically vary from -40 ° C to 120 ° C, depending upon the material. Heat-treated or glass-reinforced plastics extend thermal restrictions. Dimensional security is vital, as moisture absorption (e.g., in nylon) can change gear meshing.
** Quality assurance: ** Testing consists of dimensional examination (CMM), firmness testing, and load-cycle screening to confirm durability. Noise degrees, torque capacity, and put on resistance are assessed under substitute operating problems.
** Applications: ** Used in auto systems (window regulators, seat insurance adjusters), clinical gadgets, customer electronic devices (printers, toys), and industrial equipment where weight reduction and sound dampening are priorities.
Plastic gears call for an equilibrium of material scientific research, precision engineering, and process optimization to fulfill performance needs while preserving price performance.
(Plastic gears Design And Processing)
Applications of Plastic gears Design And Processing
Plastic gears have become indispensable components in modern design, supplying functional solutions across industries due to improvements in design and processing modern technologies. Their light-weight, rust resistance, and cost-effectiveness make them perfect for applications where metal gears deal with constraints. Among one of the most famous usages remains in the auto industry, where plastic equipments are employed in windscreen wipers, seat insurers, and cooling and heating systems. Their ability to operate silently and stand up to chemical exposure guarantees reliability in severe environments while minimizing overall vehicle weight for improved gas efficiency.
In customer electronics, plastic gears are critical for small, noise-sensitive gadgets such as printers, cams, and home devices. Their precision-molded teeth allow smooth motion control in systems like paper feeders or robotic vacuum cleaners. The use of materials like nylon or polyoxymethylene (POM) makes certain reduced rubbing and use resistance, prolonging item life expectancy. In a similar way, clinical tools leverage plastic equipments in equipment like infusion pumps and diagnostic tools, where sanitation compatibility and non-magnetic residential or commercial properties are essential.
Industrial automation additionally takes advantage of plastic equipment systems, specifically in light-duty equipment and conveyor systems. Their self-lubricating residential or commercial properties minimize maintenance demands, while injection molding allows for complicated geometries customized to particular torque and speed needs. Additionally, the aerospace and robotics sectors utilize high-performance polymers like PEEK (polyetheretherketone) for equipments that stand up to extreme temperatures and mechanical anxiety without adding too much weight.
The design of plastic gears stresses modification, with software-driven simulations enhancing tooth profiles and tons distribution. Advanced handling methods like 3D printing enable quick prototyping, while shot molding makes certain mass production uniformity. Ecological considerations better drive fostering, as recyclable thermoplastics straighten with sustainability objectives. However, engineers have to balance product option with thermal development and tons capacity limitations to ensure sturdiness.
From toys to heavy machinery, plastic gears remain to redefine movement transmission systems, combining advancement with functionality. As product science and production innovations evolve, their applications will expand, supplying quieter, lighter, and extra efficient services for tomorrow’s design challenges.
Campony Introduction
Established in 2002, Shift Gear Machinery Co.,ltd. focus on metal research and mining machinery spare parts. 2 factories over an area of 13,300 square meters, based on 100+ sets of equipment, our production capacity reaches 12000 Tons/Year. has passed ISO 9001 quality managment system certification in 2008.
Our mainly products are dragline excavator spare parts,rotary kiln spare parts, large modulus gear (gear shaft), gearbox ect. 40+ patents with over 45 years experience to help focus on improve the service life of spare parts. We belive that more than 80% reason of mechanical parts’ working life depends on hot processing (steel making/forging/casting/welding/heat treatment). Eight material engineers will control the quality from the original resource.
If you are interested, please feel free to contact us.
Payment
L/C, T/T, Western Union, Paypal, Credit Card etc.
Shipment
By sea, by air, by express, as customers request.
5 FAQs of Plastic gears Design And Processing
What are the best materials for plastic gears? The most common materials for plastic gears include nylon (PA), acetal (POM), and polycarbonate (PC). Nylon offers high wear resistance and toughness, making it ideal for high-load applications. Acetal provides low friction, high stiffness, and excellent dimensional stability, suitable for precision gears. Polycarbonate is chosen for its impact resistance and transparency. Material selection depends on factors like load capacity, operating temperature, and environmental exposure. Specialty materials like PEEK or UHMWPE may be used for extreme conditions.
How can noise be reduced in plastic gears? Noise reduction in plastic gears is achieved through precise tooth profile design, such as using involute or modified cycloidal profiles to ensure smooth meshing. Proper gear alignment, backlash control, and minimizing tooth deflection by optimizing gear geometry (e.g., module, pressure angle) also help. Adding lubricants like silicone grease or incorporating self-lubricating additives into the plastic material reduces friction-induced noise. Damping properties inherent in plastics like nylon further absorb vibrations.
What design considerations prevent plastic gear failure? Key design considerations include uniform wall thickness to avoid warping during cooling, fillets at gear root transitions to reduce stress concentrations, and accounting for thermal expansion and shrinkage in mold design. Adequate clearance between mating gears prevents overloading, while reinforcing high-stress areas with ribs or thicker sections enhances durability. Material selection must align with operational loads and environmental conditions to prevent premature wear or deformation.
Which processing methods are used for plastic gears? Injection molding is the most common method for mass-producing plastic gears due to its high precision and repeatability. For prototypes or low-volume batches, 3D printing (e.g., SLS, FDM) offers flexibility. Machining (CNC) is occasionally used for large gears or unique geometries but is less cost-effective. Post-processing steps like annealing or surface treatments may improve dimensional stability or reduce friction.
What are the advantages of plastic gears over metal gears? Plastic gears are lighter, corrosion-resistant, and operate more quietly due to inherent vibration damping. They eliminate the need for external lubrication in many cases and are cost-effective for high-volume production. Plastic gears can also be molded with integrated features like hubs or bearings, reducing assembly complexity. However, they have lower load capacity and temperature resistance compared to metal gears, making them suitable for moderate-duty applications.
(Plastic gears Design And Processing)
REQUEST A QUOTE
RELATED PRODUCTS
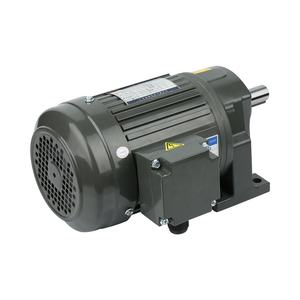
s High Precision Cnc Milling Turning Service Steel Bevel Gears Custom Spur Gears Sets

Aluminum Alloy Stainless Steel Wheel Accessories Primary Gear Wheel Bearing Gear
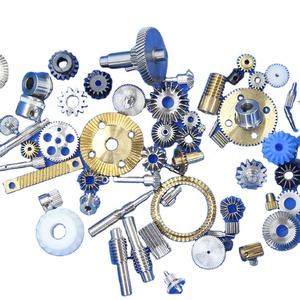
High quality and durable gear shaping cutter gear cutting durable HSS M-2 gear shaping cutter
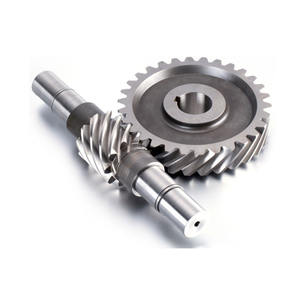
4812035018 ,4607162182,4812027192 DRIVE GEAR FOR DYNAPAC PAVER F2500CS F2530
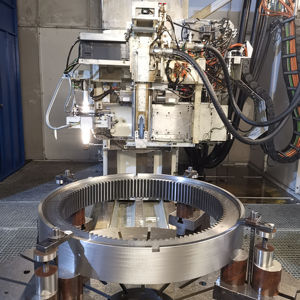
High precision custom differential bevel gears
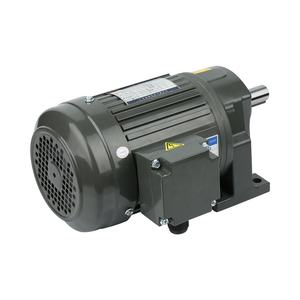