PRODUCT PARAMETERS
Description
Overview of Rotary Kiln And Cement Ball Mill Spare Pasts Wheel And Ring gear Casting Girth gear Large Steel Spur gear
Gears are mechanical elements that are typically used to transmit rotational motion and force. They work by meshing teeth with each other to change speed, direction of torque, or to transfer power between multiple shafts. Gears are an integral part of mechanical engineering and are widely used in a variety of mechanical devices.
Advantages and features of Rotary Kiln And Cement Ball Mill Spare Pasts Wheel And Ring gear Casting Girth gear Large Steel Spur gear
Efficient transmission: Gears are capable of directly converting power with high efficiency and low energy loss.
Precise ratios: the desired ratio of speed and torque can be obtained by selecting gears of different sizes.
Compact: Rotary Kiln And Cement Ball Mill Spare Pasts Wheel And Ring gear Casting Girth gear Large Steel Spur gearsystems take up less space than other forms of power transmission.
High durability: well-designed gears can operate stably for long periods of time in harsh environments.
Low noise and vibration: Modern Rotary Kiln And Cement Ball Mill Spare Pasts Wheel And Ring gear Casting Girth gear Large Steel Spur gearmanufacturing technology ensures smooth operation and reduces noise and vibration.
Various types: Spur, helical, and bevel gears are available depending on the application scenario.
(Rotary Kiln And Cement Ball Mill Spare Pasts Wheel And Ring gear Casting Girth gear Large Steel Spur gear)
Specifications of Rotary Kiln And Cement Ball Mill Spare Pasts Wheel And Ring gear Casting Girth gear Large Steel Spur gear
Rotating kiln and concrete sphere mill extra parts, including wheel and ring gear spreading, girth equipments, and big steel spur gears, are critical components crafted for sturdiness, precision, and high-performance procedure in heavy-duty industrial applications. These components are designed to stand up to severe temperature levels, mechanical stress, and rough atmospheres usual in cement production, mining, and metallurgy.
** Wheel and Ring Gear Casting: ** Produced from state-of-the-art alloy steel or ductile iron, these elements undertake warmth therapy procedures like quenching and solidifying to improve firmness (commonly 200-300 HB) and use resistance. The ring equipment size varies from 1 meter to over 8 meters, with components between 20 and 50, ensuring optimum torque transmission. Customized tooth accounts and surface area hardening techniques, such as induction or flame hardening, improve longevity under heavy lots.
** Girth Gears: ** These large-diameter equipments (up to 15 meters) are essential to rotary kilns and ball mills, including high-precision tooth flanks for smooth involvement. Constructed from ASTM A148 or hullabaloo 17200 steel, they undertake stress-relieving and machining procedures to achieve dimensional precision (AGMA 2000 or ISO 1328 standards). Face sizes vary from 500 mm to 1500 mm, with firmness degrees of 260-320 HB. Split designs assist in setup, while anti-corrosion coatings shield against severe operating problems.
** Huge Steel Stimulate Gears: ** Engineered for concrete ball mills, these gears are made from created or cast steel (grades EN 10083 or SAE 4340) with modules ranging from 30 to 60. Accuracy grinding makes sure tooth profile accuracy (AGMA Q10-Q13), decreasing resonance and sound. Warm treatment via carburizing or nitriding achieves surface area hardness of 55-62 HRC, while core toughness (220-280 HB) avoids crack under cyclic loading.
** Key Requirements: ** All equipments are custom-made to match OEM measurements, with bore diameters as much as 2000 mm and weight abilities going beyond 100 lots. Advanced NDT approaches (ultrasonic, magnetic bit) make sure defect-free spreadings. Lubrication grooves and hardened flange surfaces improve functional performance. Applications extend cement kilns, raw mills, coal mills, and slag mills, with life span going beyond ten years under proper maintenance.
These elements prioritize interchangeability, lowered downtime, and power efficiency, sustaining global cement and mining industries. Personalized metallurgy, tooth geometry, and placing setups make sure compatibility with FLSmidth, Polysius, and various other significant OEM systems. Extensive quality control and ISO 9001 qualification warranty integrity in extreme atmospheres.
(Rotary Kiln And Cement Ball Mill Spare Pasts Wheel And Ring gear Casting Girth gear Large Steel Spur gear)
Applications of Rotary Kiln And Cement Ball Mill Spare Pasts Wheel And Ring gear Casting Girth gear Large Steel Spur gear
Rotating kilns and cement ball mills are crucial parts in markets such as concrete manufacturing, mining, metallurgy, and chemical handling. Their effective operation relies heavily on top notch extra parts like wheel and ring gears, girth equipments, and big steel spur equipments. These elements guarantee dependability, sturdiness, and optimal performance in demanding industrial settings.
** Wheel and Ring Equipment Casting **.
Wheel and ring gears are essential to the rotating kiln’s drive system, transferring torque to turn the kiln drum. Manufactured from state-of-the-art alloy steels via precision casting and heat therapy procedures, these parts hold up against extreme thermal stress and anxiety, heavy lots, and unpleasant conditions. They are essential in concrete clinker manufacturing, lime calcination, and mineral processing, making certain smooth rotational motion and positioning. Custom-engineered designs improve wear resistance, reducing downtime and upkeep expenses.
** Girth Equipment for Concrete Round Mills **.
Girth equipments (additionally called ring equipments) are large-diameter gears installed on the shell of cement round mills, fitting together with pinion gears to drive the mill’s rotation. Cast from durable products like ASTM A148 steel, they endure high-impact loads and continual operation. Precision machining makes sure excellent tooth accounts for effective power transmission, important in grinding resources, clinker, and ingredients. Girth equipments are designed with advanced tooth setting techniques to decrease wear, prolonging life span in extreme milling settings. Customizable components and flanges enable seamless combination with sphere mill systems.
** Large Steel Spur Gears **.
Big steel spur gears are utilized in heavy-duty applications calling for high torque and specific motion control. These gears include straight teeth for reliable power transfer in rotating kilns, crushers, and conveyors. Forged or cast from high-strength steel alloys, they supply extraordinary load-bearing capability and resistance to deformation. Stimulate equipments are vital in mining operations, power plants, and product handling systems, where integrity and minimal reaction are extremely important.
** Applications Across Industries **.
These parts are crucial in concrete plants for pyroprocessing and grinding, in mining for ore processing, and in metallurgy for smelting and refining. Their robust building and precision engineering guarantee uninterrupted procedure, power effectiveness, and minimized operational costs. Normal upkeep and prompt replacement of these extra components avoid expensive malfunctions, enhancing the lifespan of rotary kilns and ball mills.
Purchasing high-grade wheel and ring equipments, girth gears, and spur gears warranties functional excellence, making them important for sectors prioritizing performance and durability in heavy machinery.
Campony Introduction
Established in 2002, Shift Gear Machinery Co.,ltd. focus on metal research and mining machinery spare parts. 2 factories over an area of 13,300 square meters, based on 100+ sets of equipment, our production capacity reaches 12000 Tons/Year. has passed ISO 9001 quality managment system certification in 2008.
Our mainly products are dragline excavator spare parts,rotary kiln spare parts, large modulus gear (gear shaft), gearbox ect. 40+ patents with over 45 years experience to help focus on improve the service life of spare parts. We belive that more than 80% reason of mechanical parts’ working life depends on hot processing (steel making/forging/casting/welding/heat treatment). Eight material engineers will control the quality from the original resource.
If you are interested, please feel free to contact us.
Payment
L/C, T/T, Western Union, Paypal, Credit Card etc.
Shipment
By sea, by air, by express, as customers request.
5 FAQs of Rotary Kiln And Cement Ball Mill Spare Pasts Wheel And Ring gear Casting Girth gear Large Steel Spur gear
When purchasing rotary kiln and cement ball mill spare parts like wheel and ring gear casting, girth gears, or large steel spur gears, customers often have specific questions about quality, performance, and maintenance. Here are five FAQs and their answers:
**1. What materials are used in manufacturing these gears?**
Girth gears, spur gears, and ring gears are typically cast from high-grade steel alloys, such as ASTM A148 or DIN 17200, to ensure durability under extreme mechanical stress. Heat treatment processes like quenching and tempering are applied to enhance hardness and wear resistance, ensuring longevity in high-temperature and abrasive environments.
**2. How does precision machining impact gear performance?**
Precision machining ensures optimal tooth profile accuracy, surface finish, and alignment, which minimizes friction, reduces energy consumption, and prevents premature wear. Gears must meet strict tolerances (e.g., AGMA or ISO standards) to avoid misalignment in rotary kilns or ball mills, which could lead to operational downtime.
**3. What maintenance practices extend the lifespan of these gears?**
Regular lubrication with high-viscosity oils or greases is critical to reduce metal-to-metal contact. Inspect gears periodically for cracks, pitting, or uneven wear. Align gears correctly during installation and monitor vibration levels using sensors to detect imbalances early. Protective coatings or hardening techniques like carburizing can also delay wear.
**4. What are common signs of gear failure?**
Excessive noise, vibration, or overheating during operation often indicate misalignment, insufficient lubrication, or tooth damage. Visible cracks, spalling, or tooth breakage are clear signs of failure. Sudden spikes in energy consumption may also point to inefficiencies caused by gear wear.
**5. Can these gears be customized for specific equipment?**
Yes. Manufacturers offer tailored solutions based on equipment dimensions, load capacity, and operational requirements. Customizations include adjusting module size, pressure angle, or hub design. Reverse engineering is also available for obsolete or non-standard gears to ensure compatibility with existing machinery.
These FAQs address key concerns about material quality, precision engineering, maintenance protocols, failure indicators, and customization options, helping buyers make informed decisions for reliable, long-lasting rotary kiln and ball mill gear solutions.
(Rotary Kiln And Cement Ball Mill Spare Pasts Wheel And Ring gear Casting Girth gear Large Steel Spur gear)
REQUEST A QUOTE
RELATED PRODUCTS
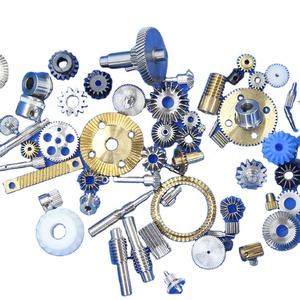
Whole Excavator Slew Slewing Motor Reduction Assy Assembly Hydraulic Swing Gearbox Parts Swing Motor
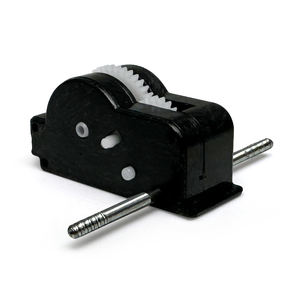
YK3608 High Efficiency Horizontal CNC Gear Hobbing Machine For Mini Gear Cutter Machine
JM JK JKL JKD gear reducer driving winch for hoisting pull and unloading tow the weight drop
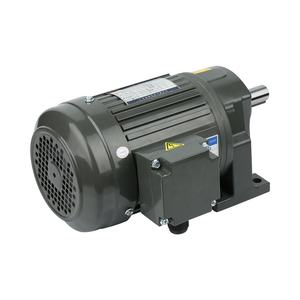
Aokman Solid Shaft Output Cyclo Gear Motor Cycloidal Gearbox for Power Industrial Transmission
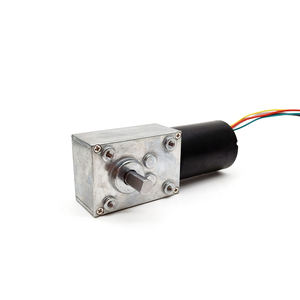
9057914 Auto parts car Gear Shift Knob Head Handle Lever Shift control handball For Buick Excelle
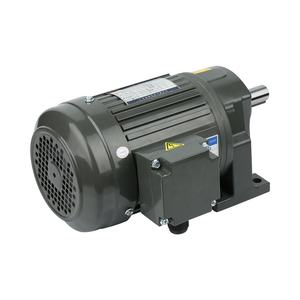